Starch-base degradable bioplastic and preparing method thereof
A bioplastic and starch-based technology, which is applied in the field of starch-based degradable bioplastics and its preparation, can solve the problems of insufficient starch hydrophobicity, pollution of plastic garbage bags, and decreased mechanical strength, and achieve improved hydrophobicity, small investment, and easy The effect of control
- Summary
- Abstract
- Description
- Claims
- Application Information
AI Technical Summary
Problems solved by technology
Method used
Examples
Embodiment 1
[0017] The preparation method of described starch-based degradable bioplastics comprises the following steps:
[0018] First dry 100kg of corn starch in a drying oven at 100°C for 4 hours, then weigh 40kg of the dried starch and add it to a mixer, and stir at 2500r / min. When the starch temperature is 80°C, the modifier The dibenzoyl peroxide solution is injected into a high mixer through a syringe and mixed with starch. The dosage of the modifier dibenzoyl peroxide solution is 0.2 kg. After stirring for 30 minutes, add 0.08 kg of nano-silica particles and continue stirring for 10 minutes. , to obtain highly hydrophobic starchy materials, then 5kg of saturated triglycerides and natural vegetable oil mixture, 5kg of zinc stearate are mixed, and made into master batches with twin-screw extruders, master batches and 50kg of polypropylene After mixing, injection molding, edge pressing, blow molding, and air molding are made into starch-based degradable bioplastics.
Embodiment 2
[0020] The preparation method of described starch-based degradable bioplastics comprises the following steps:
[0021] First dry 100kg of sorghum starch in a 110°C drying oven for 4 hours, then weigh 50kg of the dried starch and add it to a mixer, and stir at 2700r / min. When the starch temperature is 90°C, the modifier The peroxybenzoic acid solution is injected into the high mixer through a syringe and mixed with the starch. The dosage of the modifier peroxybenzoic acid solution is 0.25 kg. After stirring for 30 minutes, add 0.1 kg of nano-silicon dioxide particles, and continue stirring for 10 minutes to obtain high hydrophobicity. Starch material, then 5kg of unsaturated triglyceride and natural vegetable oil mixture, 5kg of manganese stearate are mixed, and made into masterbatch with a twin-screw extruder, after the masterbatch is mixed with 40kg of polystyrene , Injection molding, edge pressing, blow molding, and air molding are made into starch-based degradable bioplasti...
Embodiment 3
[0023] The preparation method of described starch-based degradable bioplastics comprises the following steps:
[0024] Dry 100kg of potato starch in a drying oven at 120°C for 4 hours first, then weigh 35kg of the dried starch and add it to a mixer, and stir at 3000r / min. When the starch temperature is 100°C, the modifier The cumene hydrogen peroxide solution is injected into the high mixer through a syringe and mixed with the starch. The amount of the modifier cumene hydrogen peroxide solution is 0.175 kg. After stirring for 30 minutes, add 0.07 kg of nano-silica particles and continue stirring for 10 minutes. , to obtain highly hydrophobic starchy material, then the monoglyceride and triglyceride mixture of 2.5 unsaturated fatty acids, the oleate of zinc of 2.5kg are mixed, make master batch with twin-screw extruder, master batch and After 60kg of polyvinyl chloride is mixed, injection molding, edge pressing, blow molding, and air molding are made into starch-based degradabl...
PUM
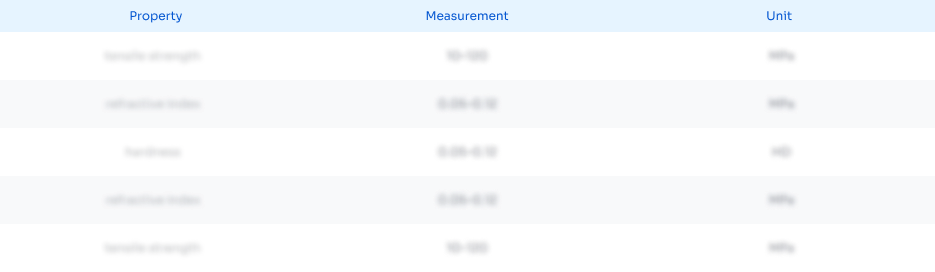
Abstract
Description
Claims
Application Information

- Generate Ideas
- Intellectual Property
- Life Sciences
- Materials
- Tech Scout
- Unparalleled Data Quality
- Higher Quality Content
- 60% Fewer Hallucinations
Browse by: Latest US Patents, China's latest patents, Technical Efficacy Thesaurus, Application Domain, Technology Topic, Popular Technical Reports.
© 2025 PatSnap. All rights reserved.Legal|Privacy policy|Modern Slavery Act Transparency Statement|Sitemap|About US| Contact US: help@patsnap.com