Method for preparing master batches through direct PET melt mixing and equipment special for method
A special equipment and melt technology, which is applied in the field of direct mixing of PET melt to produce masterbatch, can solve the problems of insignificant viscosity reduction, melt viscosity reduction, and complicated process, so as to improve the quality of masterbatch, reduce viscosity drop, cost reduction effect
- Summary
- Abstract
- Description
- Claims
- Application Information
AI Technical Summary
Problems solved by technology
Method used
Image
Examples
Embodiment 1
[0027] Embodiment 1 A kind of PET melt of the present invention directly mixes and prepares the method for masterbatch, comprises the steps:
[0028] Step 1. Introduce a melt with a viscosity of 0.63dl / g from the PET main melt pipeline, and mix in matting agent (49%) and dispersant (1%) according to the mass ratio to obtain a compound; mix in matting agent and dispersant in proportion , to obtain the mixture, the mass ratio of the melt: matting agent: dispersant is 1:0.49:0.01; the melt is PET, the matting agent is titanium dioxide, and the dispersant is titanic acid Ester coupling agent;
[0029]Step 2. The mixture obtained in step 1 is entered into a twin-screw extruder under negative pressure for low-speed (120rpm) initial mixing to form an initial mixing melt;
[0030] Step 3. The primary mixed melt coming out of the twin-screw extruder is first blended by an ultrasonic dynamic mixer to obtain a miscible body;
[0031] Step 4. Water-cool the mixed melt from the ultrasoni...
Embodiment 2
[0033] Example 2 The special equipment constructed by the method described in Example 1, including extruder assembly 1, auxiliary material bin assembly 2, dispersant bin assembly 3, ultrasonic dynamic mixing assembly 4, pelletizing assembly 5 , dry packer 6 and control box, the main melt pipeline 7 is connected on the outlet of the discharge assembly 8, and the main melt pipeline 7 is connected with the extruder assembly 1 through the branch melt pipeline 71 The first feed port of the dispersant bin assembly 3 is connected to the first feed port, the discharge port of the auxiliary material bin assembly 2 is configured with the first feed material assembly 91, and the discharge port of the dispersant bin assembly 3 is configured with the second feed material assembly. 92, and the discharge port of the first feeding assembly 91 and the second feeding assembly 92 are all in communication with the second feeding port pipeline of the extruder assembly 1, the extruder assembly 1 Th...
Embodiment 3
[0049] Example 3 Contrast of conventional masterbatch preparation and melt preparation masterbatch
[0050] 1. Case of conventional masterbatch production: carrier PET, matting masterbatch, output 3 tons / day:
[0051] The carrier purchased by the masterbatch factory is PET high-viscosity chips (the chips are made through polymerization, pelletizing, drying, and solid-state polycondensation), with a viscosity of 0.82dl / g. The carrier is first ground into a diameter of about 500 mesh by a mill. Utilize powder metering to send 40% matting agent (TiO2), 59% carrier powder and 1% dispersant into twin-screw extruder (length-to-diameter ratio is 44), twin-screw rotating speed is 300rpm, comes out from screw extruder The melt is water-cooled, pelletized, dried and packaged, and the viscosity of the masterbatch is 0.40dl / g.
[0052] 2. Melt masterbatch production case: carrier PET, matting masterbatch, output 3 tons / day:
[0053]The melt with a viscosity of 0.62dl / g is introduced fr...
PUM
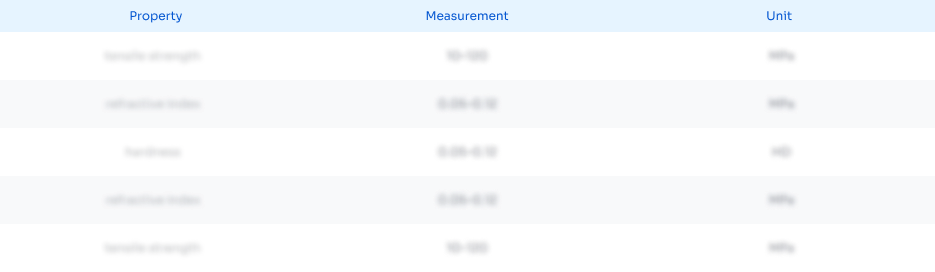
Abstract
Description
Claims
Application Information

- R&D
- Intellectual Property
- Life Sciences
- Materials
- Tech Scout
- Unparalleled Data Quality
- Higher Quality Content
- 60% Fewer Hallucinations
Browse by: Latest US Patents, China's latest patents, Technical Efficacy Thesaurus, Application Domain, Technology Topic, Popular Technical Reports.
© 2025 PatSnap. All rights reserved.Legal|Privacy policy|Modern Slavery Act Transparency Statement|Sitemap|About US| Contact US: help@patsnap.com