Method for directly synthesizing 2,2,4-trimethyl-1,3-pentanediol diisobutyrate from isobutyraldehyde
A technology of pentylene glycol diisobutyrate and pentylene glycol monoisobutyrate, which is applied to the preparation of carboxylic acid esters, chemical instruments and methods, and the preparation of organic compounds, and can solve the high cost of separation and purification and potential safety hazards and other problems, to achieve the effect of low price, simplified operation process, and cheap and easy-to-obtain raw materials
- Summary
- Abstract
- Description
- Claims
- Application Information
AI Technical Summary
Problems solved by technology
Method used
Image
Examples
Embodiment 1
[0031] The method for directly synthesizing 2,2,4-trimethyl-1,3-pentanediol diisobutyrate by isobutyraldehyde, the steps are as follows:
[0032] (1) In the tank reactor with stirring and temperature control system, add 1 part by weight of basic catalyst NaOH, and slowly add 50 parts by weight of isobutyraldehyde dropwise under stirring conditions, and control the temperature at 40 ° C Carry out aldol condensation reaction and disproportionation into ester reaction to obtain a reaction solution of 2,2,4-trimethyl-1,3-pentanediol monoisobutyrate and unreacted isobutyraldehyde; the reaction time is 5 hours , the conversion rate of isobutyraldehyde in aldol condensation reaction and disproportionation into ester reaction is controlled at 62.1%.
[0033] (2) NaOH in the reaction solution is filtered out, and the oxidation catalyst MnO is added to the reactor 2 Afterwards, the oxidant air is passed into the reaction kettle, and the temperature is controlled at 60° C., and the reac...
Embodiment 2
[0037] The method for directly synthesizing 2,2,4-trimethyl-1,3-pentanediol diisobutyrate by isobutyraldehyde, the steps are as follows:
[0038] (1) In the tank reactor with stirring, temperature control system, add the basic catalyst Ca(OH) of 4 parts by weight 2 , under stirring conditions, slowly add 200 parts by weight of isobutyraldehyde dropwise, and control the temperature at 80°C for aldol condensation reaction and disproportionation into ester reaction to obtain 2,2,4-trimethyl-1,3-pentane The reaction solution of diol monoisobutyrate and unreacted isobutyraldehyde; the reaction time is 3 hours, and the conversion rate of isobutyraldehyde in aldol condensation reaction and disproportionation into ester reaction is controlled to be 63.6%.
[0039] (2) Ca(OH) in the reaction solution 2 Filter out, and add oxidation catalyst MnO to the reactor 2 After that, add the oxidant hydrogen peroxide to the reaction kettle, control the temperature at 60°C, and react for 5 hours...
Embodiment 3
[0043] The method for directly synthesizing 2,2,4-trimethyl-1,3-pentanediol diisobutyrate by isobutyraldehyde, the steps are as follows:
[0044] (1) In the tank reactor with stirring and temperature control system, add 2 parts by weight of basic catalyst Na 2 O, under stirring conditions, slowly add 200 parts by weight of isobutyraldehyde dropwise, and control the temperature to carry out aldol condensation reaction and disproportionation into ester reaction at 60°C to obtain 2,2,4-trimethyl-1,3- The reaction solution of pentanediol monoisobutyrate and unreacted isobutyraldehyde; the reaction time is 2 hours, and the conversion rate of isobutyraldehyde in aldol condensation reaction and disproportionation into ester reaction is controlled to be 67.3%.
[0045] (2) Na in the reaction liquid 2 O is filtered out and the oxidation catalyst Fe is added to the reactor 2 o 3 Afterwards, feed oxidant oxygen into the reactor, control the temperature at 100°C, and react for 7 hours ...
PUM
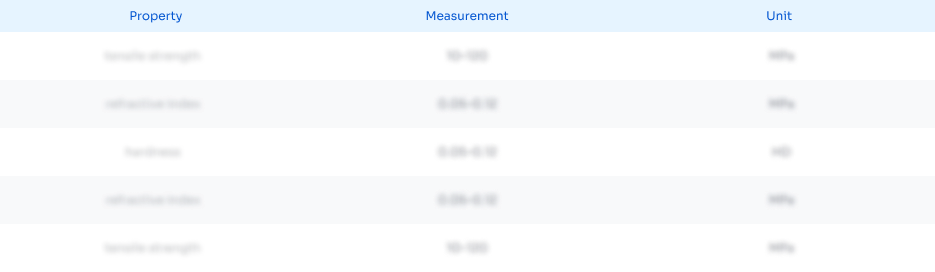
Abstract
Description
Claims
Application Information

- R&D
- Intellectual Property
- Life Sciences
- Materials
- Tech Scout
- Unparalleled Data Quality
- Higher Quality Content
- 60% Fewer Hallucinations
Browse by: Latest US Patents, China's latest patents, Technical Efficacy Thesaurus, Application Domain, Technology Topic, Popular Technical Reports.
© 2025 PatSnap. All rights reserved.Legal|Privacy policy|Modern Slavery Act Transparency Statement|Sitemap|About US| Contact US: help@patsnap.com