Building ceramsite using coke gem tailings as raw material and preparation method thereof
A technology of coke gem tailings and raw materials, which is applied in the field of construction ceramsite and its preparation, can solve the problems of low alumina content in tailings, unsuitability for refractory materials, and damage to the ecological environment, and achieve low bulk density and simple and easy production process Understand the effect of simple production process
- Summary
- Abstract
- Description
- Claims
- Application Information
AI Technical Summary
Problems solved by technology
Method used
Examples
Embodiment 1
[0037] The construction ceramsite with coke gem tailings as raw material, the raw materials of ultra-low density ceramsite proppant by weight percentage are: coke gem tailings 60%, carbon powder 40%
[0038] Preparation method of building ceramsite using coke gem tailings as raw material:
[0039] (1) uniformly mix coke gem tailings and carbon powder in proportion to obtain a mixed material;
[0040] (2) The mixed material is added to the quick grinder, water of 40%wt of the mixed material, 0.3%wt binder sodium polyacrylate of the mixed material and 0.3%wt dispersant CMC of the mixed material are added, and the mixed material is ball milled to 900 order, to obtain slurry;
[0041] (3) The slurry is spray-dried by a spray dryer to obtain a powder;
[0042] (4) 5Kg powder is added to the disc granulator, and the moisture of 20%wt is evenly added using a spray gun to carry out mixing and granulation, and the prepared pellets are sieved to obtain semi-finished pellets;
[0043]...
Embodiment 2
[0046] Raw materials of ultra-low-density ceramsite proppant by weight percentage: 70% of coke gem tailings, 30% of carbon powder
[0047] Preparation method of building ceramsite using coke gem tailings as raw material:
[0048] (1) uniformly mix coke gem tailings and starch in proportion to obtain a mixed material;
[0049] (2) The mixed material is added to the quick grinder, water of 40%wt of the mixed material, 0.3%wt binder sodium polyacrylate of the mixed material and 0.3%wt dispersant CMC of the mixed material are added, and the mixed material is ball milled to 900 order, to obtain slurry;
[0050] (3) The slurry is spray-dried by a spray dryer to obtain a powder;
[0051] (4) 5Kg powder is added to the granulator, and the moisture of 20%wt is evenly added using a spray gun to carry out mixing and granulation, and the prepared pellets are sieved to obtain semi-finished pellets;
[0052] (5) Dry the semi-finished pellets at 120°C for 12 hours;
[0053] (6) Finally, ...
Embodiment 3
[0055] Raw materials of ultra-low-density ceramsite proppant by weight percentage: 80% of coke gem tailings, 20% of carbon powder
[0056] Preparation method of building ceramsite using coke gem tailings as raw material:
[0057] (1) uniformly mix coke gem tailings and starch in proportion to obtain a mixed material;
[0058] (2) The mixed material is added to the quick grinder, water of 40%wt of the mixed material, 0.3%wt binder sodium polyacrylate of the mixed material and 0.3%wt dispersant CMC of the mixed material are added, and the mixed material is ball milled to 900 order, to obtain slurry;
[0059] (3) The slurry is spray-dried by a spray dryer to obtain a powder;
[0060] (4) 5Kg powder is added to the granulator, and the moisture of 20%wt is evenly added using a spray gun to carry out mixing and granulation, and the prepared pellets are sieved to obtain semi-finished pellets;
[0061] (5) Dry the semi-finished pellets at 120°C for 12 hours;
[0062] (6) Finally, ...
PUM
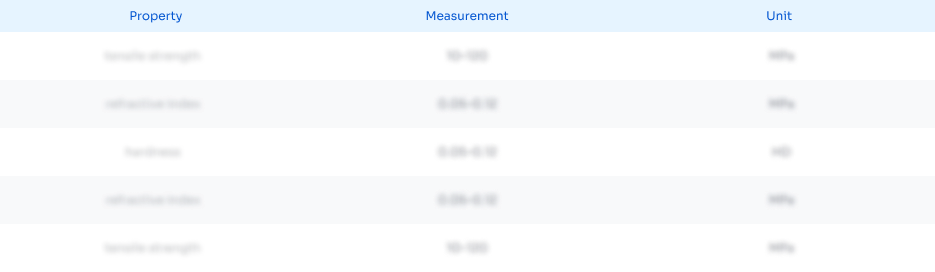
Abstract
Description
Claims
Application Information

- Generate Ideas
- Intellectual Property
- Life Sciences
- Materials
- Tech Scout
- Unparalleled Data Quality
- Higher Quality Content
- 60% Fewer Hallucinations
Browse by: Latest US Patents, China's latest patents, Technical Efficacy Thesaurus, Application Domain, Technology Topic, Popular Technical Reports.
© 2025 PatSnap. All rights reserved.Legal|Privacy policy|Modern Slavery Act Transparency Statement|Sitemap|About US| Contact US: help@patsnap.com