High-performance organic rectorite used for oil-based drilling fluids and a producing method thereof
A technology of oil-based drilling fluid and production method, which is applied in the direction of chemical instruments and methods, drilling compositions, etc., can solve the problems of unimproved product formula composition, affecting the effect of organicization, and affecting the effect of organicization, so as to achieve compensation Insufficient cation exchange capacity, stable comprehensive performance, excellent effect of high temperature stability
- Summary
- Abstract
- Description
- Claims
- Application Information
AI Technical Summary
Problems solved by technology
Method used
Image
Examples
Embodiment 1
[0029] Using calcium-based rectorite raw ore with a rectorite grade of 45% as raw material, the rectorite concentrate is obtained through primary crushing-scrubbing-mashing-screwing-hydrocyclone-dense sedimentation and other separation steps. The content is 75%, dried and crushed to 100 mesh for later use.
[0030] In the reaction vessel, add 100 parts of calcium-based rectorite powders (100 meshes) containing 75% rectorite and 6% water content through selection, add 2 parts of sodium carbonate, 1.5 parts of lithium carbonate, Add 200 parts of water to the mixed solution of 200 parts of water, heat and stir at a speed of 120 rpm, and raise the temperature to 90°C. Keep stirring for 45 minutes, take 35 parts of octadecyldimethylbenzyl ammonium chloride with a net content of 70%, add it to the container, keep the temperature of the container at 90°C, continue stirring at a speed of 120 rpm, and carry out organic reaction for 90 minutes. Stop the reaction, add 200 parts of water...
Embodiment 2
[0032]Using the rectorite concentrate with a purity of 75% obtained in Example 1 as a raw material, the rectorite with a purity of 90% was obtained through the steps of ultra-fine crushing-polyphosphate dispersion-stirring-centrifugation and other steps , dried and crushed to 100 mesh for later use. The specific purification route is to add 100 parts of rectorite concentrate with a purity of 75% to 800 meshes to 1400 parts of water, then add 2.8 parts of sodium hexametaphosphate to it, and place it in a mixing tank for linear speed of 8.5 Stir at m / s for 60 minutes to form a uniformly dispersed suspension, and then place the suspension in a centrifuge for centrifugation. The separation factor is 3200, and the separation time is 1.5 minutes. suspend the rectorite slurry, then dehydrate, dry and pulverize the suspension slurry to obtain a purified rectorite product with a purity of 90% and an equilibrium water content of 6%.
[0033] In the reaction vessel, add 100 parts of cal...
Embodiment 3
[0035] Using the rectorite with a purity of 75% obtained in Example 1 as a raw material, through polyphosphate dispersion-stirring-centrifugation, increasing the separation factor and prolonging the centrifugation time, the rectorite with a purity of 95% was obtained. stone, dried and crushed to 100 mesh for later use.
[0036] The specific purification route is that the rectorite concentrate with a purity of 75% is ultra-finely crushed to 800 mesh, 100 parts are added to 1900 parts of water, and 3.5 parts of sodium hexametaphosphate is added to it, and placed in a mixing tank for linear speed After stirring for 60 minutes at 8.5m / s, a uniformly dispersed suspension is formed, and then the suspension is placed in a centrifuge for centrifugation. The separation factor is 3300, and the separation time is 2 minutes. Tailings and purified The rectorite suspension slurry is then dehydrated, dried and pulverized to obtain a purified rectorite product with a purity of 95% and an equi...
PUM
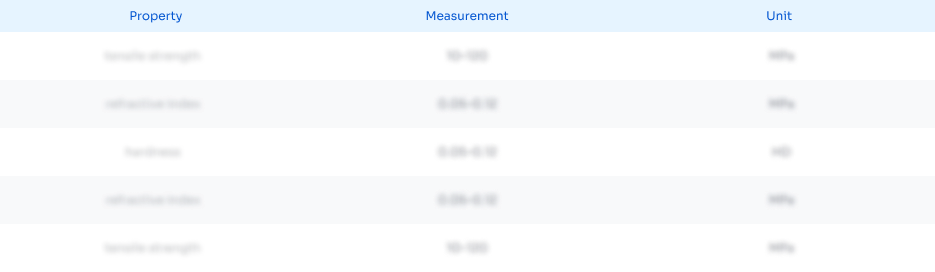
Abstract
Description
Claims
Application Information

- R&D
- Intellectual Property
- Life Sciences
- Materials
- Tech Scout
- Unparalleled Data Quality
- Higher Quality Content
- 60% Fewer Hallucinations
Browse by: Latest US Patents, China's latest patents, Technical Efficacy Thesaurus, Application Domain, Technology Topic, Popular Technical Reports.
© 2025 PatSnap. All rights reserved.Legal|Privacy policy|Modern Slavery Act Transparency Statement|Sitemap|About US| Contact US: help@patsnap.com