Feedforward control method for cold rolled strip shape
A feed-forward control, cold-rolled strip technology, applied in the field of strip rolling, can solve the problem of not considering the strip shape stability at the entrance of the rolling mill and the influence of the strip shape at the exit of the rolling mill
- Summary
- Abstract
- Description
- Claims
- Application Information
AI Technical Summary
Problems solved by technology
Method used
Image
Examples
Embodiment 1
[0047] (1) Strip shape detection at the entrance of the rolling mill
[0048] Such as figure 1 As shown, the strip single-stand reversible cold rolling unit includes an entrance uncoiler / coiler 11, an entrance turning roll 21, an entrance contact pressure shape meter 31, a 20-roll mill 4, an exit contact pressure shape meter 32, and an exit turning roll Roller 22, exit uncoiler / coiler 12. Among them, the plate shape actuators owned by the 20-roll rolling mill 4 here include: 7 back-up roll crown adjustment mechanisms ASU 1 、ASU 2 ,...,ASU 7 , the upper and lower first intermediate roller axial movement mechanism SHIFT upper 、SHIFT down .
[0049] In this embodiment, the strip shape gauges at the entrance and exit of the rolling mill respectively detect and track and record the strip shape at the entrance and exit of the rolling mill and the corresponding length positions in real time.
[0050] (2) Calculation of feedforward shape deviation
[0051] For the first rollin...
Embodiment 2
[0114] The method of the present invention is applied to a newly added flatness automatic control system of a stainless steel 20-roll cold rolling mill. The system has a flatness feedback control function module and a flatness feedforward control function module, and one of the flatness control modules can be selected and input according to actual production needs. The shape control function module, or put into two shape control function modules at the same time. A set of contact pressure shapers are installed at the entrance and exit of the cold rolling mill of this unit.
[0115] For 300-series stainless steel, the inlet thickness is 2.6mm, the width is 1260mm, and the outlet thickness is 0.35mm. The simulation results of the shape system show that for this type of steel coil, such as image 3 As shown, before and after using the method of the present invention, the 6I-UNIT hit rates of strip shape deviation at the exit of the rolling mill are 96% and 99% respectively, indi...
PUM
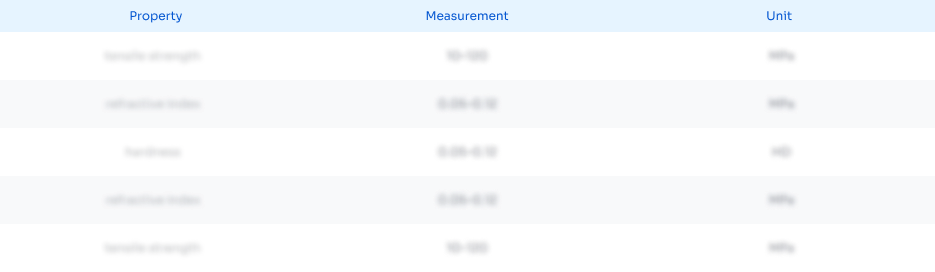
Abstract
Description
Claims
Application Information

- Generate Ideas
- Intellectual Property
- Life Sciences
- Materials
- Tech Scout
- Unparalleled Data Quality
- Higher Quality Content
- 60% Fewer Hallucinations
Browse by: Latest US Patents, China's latest patents, Technical Efficacy Thesaurus, Application Domain, Technology Topic, Popular Technical Reports.
© 2025 PatSnap. All rights reserved.Legal|Privacy policy|Modern Slavery Act Transparency Statement|Sitemap|About US| Contact US: help@patsnap.com