Aqueous dry lamination adhesive and preparation method thereof
A film-coating adhesive and dry-type technology, which is applied in adhesive types, rosin adhesives, ester copolymer adhesives, etc., can solve the problems that acrylic emulsions cannot balance adhesion, initial adhesion, and peel strength. Achieve the effects of improving adhesion and peel strength, excellent initial tack, and wide application
- Summary
- Abstract
- Description
- Claims
- Application Information
AI Technical Summary
Problems solved by technology
Method used
Image
Examples
Embodiment 1
[0017] The preparation method of the water-based dry-type film-coating adhesive in this example is prepared as follows:
[0018] (1) Mix 25 parts of styrene, 40 parts of butyl acrylate and 2 parts of hydroxyethyl acrylate to obtain mixed monomer A solution; 4 parts of N-methylolacryloyl, 3.5 parts of acrylic acid and 20 parts of deionized water Mix uniformly to obtain a mixed monomer B solution; 20 parts of styrene, 55 parts of butyl acrylate, 35 parts of isooctyl acrylate, 5 parts of acrylonitrile and 12 parts of rosin are mixed uniformly to obtain a mixed monomer C solution;
[0019] (2) Mix 180 parts of deionized water, 3 parts of isooctylphenol polyoxyethylene ether, 0.8 parts of sodium dodecylbenzenecyclonate and 10%-15% of monomers A and B in step (1) Add the solution into the reaction kettle, stir and heat up to 70±2°C to obtain a mixed solution, add 0.3 parts of buffer and 0.2 parts of potassium persulfate into the reaction kettle, control the temperature at 75±1°C, an...
Embodiment 2
[0024] The preparation method of the water-based dry-type film-coating adhesive in this example is prepared as follows:
[0025] (1) Mix 28 parts of styrene, 48 parts of butyl acrylate, 3 parts of hydroxyethyl acrylate and 3 parts of acrylonitrile to obtain a mixed monomer A solution; 5 parts of N-methylolacryloyl, 6 parts of acrylic acid and 40 parts of deionized water were mixed uniformly to obtain mixed monomer B solution; 25 parts of styrene, 65 parts of butyl acrylate, 25 parts of isooctyl acrylate, 6 parts of acrylonitrile and 15 parts of rosin were mixed uniformly to obtain mixed monomer C solution ;
[0026] (2) Mix monomers A and B with 200 parts of deionized water, 4.0 parts of isooctylphenol polyoxyethylene ether, 1.4 parts of sodium dodecylbenzenecyclonate and 10%-15% in step (1) Add the solution into the reaction kettle, stir and heat up to 70±2°C to obtain a mixed solution, add 0.4 parts of buffer and 0.3 parts of potassium persulfate into the reaction kettle, c...
Embodiment 3
[0031] The preparation method of the water-based dry-type film-coating adhesive in this example is prepared as follows:
[0032] (1) Mix 30 parts of styrene, 55 parts of butyl acrylate, 5 parts of hydroxyethyl acrylate and 5 parts of acrylonitrile to obtain a mixed monomer A solution; 6 parts of N-methylol acryloyl, 8 parts of acrylic acid and 50 parts of deionized water were mixed uniformly to obtain mixed monomer B solution; 35 parts of styrene, 75 parts of butyl acrylate, 40 parts of isooctyl acrylate, 8 parts of acrylonitrile and 25 parts of rosin were mixed uniformly to obtain mixed monomer C solution ;
[0033] (2) Mix monomers A and B with 220 parts of deionized water, 4.8 parts of isooctylphenol polyoxyethylene ether, 1.8 parts of sodium dodecylbenzenecyclonate and 10%-15% in step (1) Add the solution into the reaction kettle, stir and heat up to 70±2°C to obtain a mixed solution, add 0.5 parts of buffer and 0.4 parts of potassium persulfate into the reaction kettle, ...
PUM
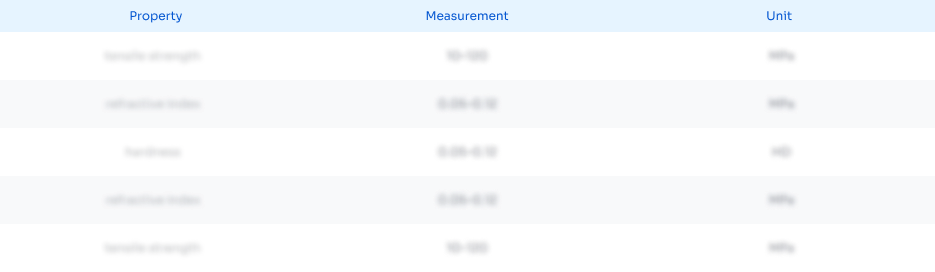
Abstract
Description
Claims
Application Information

- Generate Ideas
- Intellectual Property
- Life Sciences
- Materials
- Tech Scout
- Unparalleled Data Quality
- Higher Quality Content
- 60% Fewer Hallucinations
Browse by: Latest US Patents, China's latest patents, Technical Efficacy Thesaurus, Application Domain, Technology Topic, Popular Technical Reports.
© 2025 PatSnap. All rights reserved.Legal|Privacy policy|Modern Slavery Act Transparency Statement|Sitemap|About US| Contact US: help@patsnap.com