Acrylic acid modified polysiloxane resin and application thereof to self-stratifying coating
A polysiloxane resin, acrylic technology, applied in anti-corrosion coatings and other directions, can solve problems such as poor weather resistance and long-term effect, achieve good anti-corrosion and weather resistance, obvious cost advantages, and improve the effect of anti-corrosion and weather resistance
- Summary
- Abstract
- Description
- Claims
- Application Information
AI Technical Summary
Problems solved by technology
Method used
Image
Examples
Embodiment 1
[0031] Add 700g of solvent butyl acetate to the reactor, stir and heat up to 120°C, reflux for 15 minutes, start to add dropwise 800g of methyl methacrylate, 460g of hydroxyethyl acrylate, 40g of methacrylic acid, 150g of n-butyl acrylate, styrene 390g, a mixed solution of 160g of γ-methacryloxypropylmethyldimethoxysilane and 50g of initiator azobisisobutyronitrile, drop it in 3 hours, keep the temperature of the dropping process at 120°C, drop it After 2 hours of heat preservation, 10g of azobisisobutyronitrile (dissolved in 200g of butyl acetate) was added, further heat preservation was carried out for 1 hour, and finally 300g of butyl acetate was added, and the material was discharged to obtain propionic acid modified silicone resin-A.
Embodiment 2
[0033] Add 700g of solvent butyl acetate to the reactor, stir and heat up to 120°C, reflux for 15 minutes, start to add dropwise 750g of methyl methacrylate, 460g of hydroxyethyl acrylate, 40g of methacrylic acid, 190g of n-butyl acrylate, styrene 260g, a mixed solution of 300g of γ-methacryloxypropylmethyldimethoxysilane and 50g of initiator azobisisobutyronitrile, drop it in 3 hours, keep the temperature of the dropping process at 120°C, After 2 hours of heat preservation, 10 g of azobisisobutyronitrile (dissolved in 200 g of butyl acetate) was added, further heat preservation was carried out for 1 hour, and finally 300 g of butyl acetate was added and discharged to obtain propionic acid modified silicone resin-B.
Embodiment 3
[0035] Add 700g of solvent butyl acetate to the reactor, stir and heat up to 120°C, reflux for 15 minutes, start to add dropwise 750g of methyl methacrylate, 460g of hydroxyethyl acrylate, 40g of methacrylic acid, 190g of n-butyl acrylate, styrene 260g, a mixed solution of 300g vinyltriisopropoxysilane and 50g initiator azobisisobutyronitrile, drop it in 3 hours, keep the temperature of the dropping process at 120°C, keep warm for 2 hours after dropping, add 10g azobisisobutyronitrile Azodiisobutyronitrile (dissolved in 200g butyl acetate), keep warm for 1h, and finally add 300g butyl acetate before discharging. Propionic acid-modified silicone resin-C was obtained.
PUM
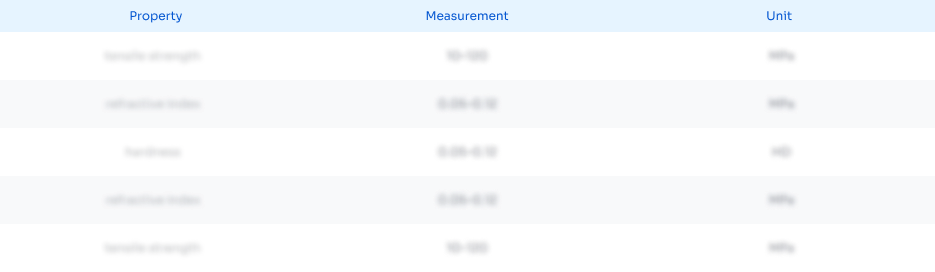
Abstract
Description
Claims
Application Information

- R&D
- Intellectual Property
- Life Sciences
- Materials
- Tech Scout
- Unparalleled Data Quality
- Higher Quality Content
- 60% Fewer Hallucinations
Browse by: Latest US Patents, China's latest patents, Technical Efficacy Thesaurus, Application Domain, Technology Topic, Popular Technical Reports.
© 2025 PatSnap. All rights reserved.Legal|Privacy policy|Modern Slavery Act Transparency Statement|Sitemap|About US| Contact US: help@patsnap.com