Rapid hardening early strength type foam concrete and preparation method thereof
A foamed concrete, early-strength technology, applied in the field of engineering materials, can solve the problems of reduced application efficiency, long setting time, difficult analysis, etc., to optimize the internal pore structure, increase the scope of use, and reduce the number of foams.
- Summary
- Abstract
- Description
- Claims
- Application Information
AI Technical Summary
Problems solved by technology
Method used
Image
Examples
Embodiment 1
[0035] A preparation method of rapid hardening and early strength foam concrete, comprising the following steps:
[0036] Step 1 Use 70% by mass of P×Ⅱ42.5 grade Portland cement and 30% of CA-60 aluminate cement to make composite cement, use 5% stearic acid, 20% ethylene-vinyl acetate and 75% styrene-butadiene emulsion to synthesize polymer emulsion; 20% by mass of composite cement, 19.2% of water, 5% of b-hemihydrate gypsum, 20% of grade I fly ash, 15% of S105 active Mineral powder, 5% agglomerated silica fume, 15% polymer emulsion, 0.2% polypropylene fiber, 0.5% polycarboxylate superplasticizer, 0.1% cellulose ether in the slurry mixing drum at 180r / Stir at a speed of 1 min to form a slurry material and quickly disperse and stir evenly;
[0037] Step 2. After 45 seconds, the dispersed clean slurry is automatically pumped into the foam mixing cylinder by the pump. At the same time, according to the bulk density of the foam concrete, the foaming agent with a mass percentage ...
Embodiment 2
[0044] A preparation method of rapid hardening and early strength foam concrete, comprising the following steps:
[0045]Step 1 Use 50% by mass of P×Ⅱ52.5 grade Portland cement and 50% of CA-50 aluminate cement to make composite cement, use 10% stearic acid, 28% ethylene-vinyl acetate and 62% styrene-butadiene emulsion to synthesize polymer emulsion; 36% by mass of composite cement, 23.3% of water, 10% of b-hemihydrate gypsum, 13% of grade I fly ash, 8% of S105 activity Mineral powder, 3% agglomerated silica fume, 6% polymer emulsion, 0.1% polypropylene fiber, 0.4% polycarboxylate superplasticizer, 0.2% cellulose ether in the slurry mixing drum at 180r / Stir at a speed of 1 min to form a slurry material and quickly disperse and stir evenly;
[0046] Step 2. After 45 seconds, the dispersed clean slurry is automatically pumped into the foam mixing cylinder by the pump. At the same time, according to the bulk density of the foam concrete, the foaming agent with a mass percentage...
Embodiment 3
[0053] A preparation method of rapid hardening and early strength foam concrete, comprising the following steps:
[0054] Step 1 Use 60% by mass of P×Ⅱ42.5 grade Portland cement and 40% of CA-50 aluminate cement to make composite cement, use 7% stearic acid, 24% ethylene-vinyl acetate Synthetic polymer emulsion with 69% styrene-butadiene emulsion; 30% by mass of composite cement, 20.2% of water, 8% of b-hemihydrate gypsum, 15% of grade I fly ash, 12% of S105 activity Mineral powder, 4% agglomerated silica fume, 10% polymer emulsion, 0.05% polypropylene fiber, 0.3% polycarboxylate superplasticizer, 0.05% cellulose ether in the slurry mixing drum at 180r / Stir at a speed of 1 min to form a slurry material and quickly disperse and stir evenly;
[0055] Step 2. After 45 seconds, the dispersed clean slurry is automatically pumped into the foam mixing cylinder by the pump. At the same time, according to the bulk density of the foam concrete, the foaming agent with a mass percentage...
PUM
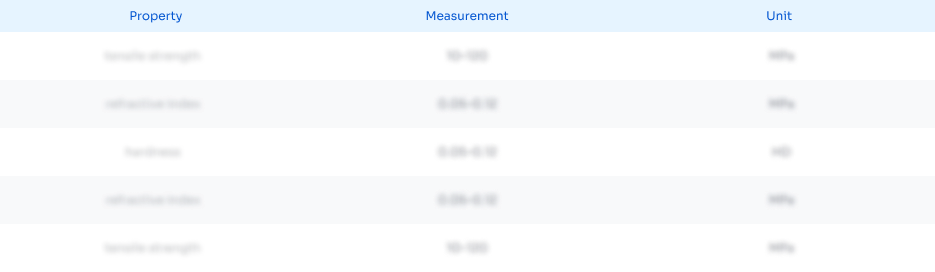
Abstract
Description
Claims
Application Information

- R&D Engineer
- R&D Manager
- IP Professional
- Industry Leading Data Capabilities
- Powerful AI technology
- Patent DNA Extraction
Browse by: Latest US Patents, China's latest patents, Technical Efficacy Thesaurus, Application Domain, Technology Topic, Popular Technical Reports.
© 2024 PatSnap. All rights reserved.Legal|Privacy policy|Modern Slavery Act Transparency Statement|Sitemap|About US| Contact US: help@patsnap.com