A kind of smelting method of high aluminum nitride steel
A high-aluminum nitrided steel and nitrided steel technology, applied in the field of alloy structural steel, can solve the problems of increasing difficulty in controlling non-metallic inclusions, common and serious slag and nodules, unstable aluminum yield, etc., reaching Optimize the timing of joining, improve the effect of slag removal, and reduce the effect of bare area and probability
- Summary
- Abstract
- Description
- Claims
- Application Information
AI Technical Summary
Problems solved by technology
Method used
Examples
Embodiment 1
[0018] High aluminum nitride steel is produced by the process route of EAF-CONVERTER electric converter smelting→LF furnace refining→VD vacuum treatment→CCM continuous casting:
[0019] The total charge of the electric converter is controlled at 101.46 tons, the molten iron ratio is 90%, the pig iron addition is 3.2 tons, and the rest is high-quality steel scrap. Tapping end point composition C: 0.12%, P: 0.008%, tapping temperature T: 1642°C, tapping volume 87.2 tons; adding 120kg of Al blocks and 110kg of calcium carbide for deoxidation, adding 455kg of silicomanganese and 2148kg of high-carbon ferrochrome And 250kg of ferromolybdenum for post-furnace alloying, and add 800kg of lime and 300kg of low-silicon synthetic slag for slagging;
[0020] In the early stage of LF refining, 80kg of aluminum particles and 30kg of silicon carbide were used to strengthen deoxidation, the pressure of bottom blowing argon gas was adjusted to 0.45MPa, and the white slag was realized after 8 m...
Embodiment 2
[0026] High aluminum nitride steel is produced by the process route of EAF-CONVERTER electric converter smelting→LF furnace refining→VD vacuum treatment→CCM continuous casting:
[0027] The total charge of the electric converter is controlled at 100.62 tons, the molten iron ratio is 91%, the pig iron addition is 2.9 tons, and the rest is high-quality steel scrap. Tapping end point composition C: 0.15%, P: 0.009%, tapping temperature T: 1649°C, tapping volume 86.8 tons; adding 150kg of Al blocks and 100kg of calcium carbide for deoxidation during tapping, adding 450kg of silicomanganese and 2150kg of high-carbon ferrochrome And 260kg of ferromolybdenum for post-furnace alloying, and add 750kg of lime and 200kg of low-silicon synthetic slag for slagging;
[0028] In the early stage of LF refining, 70kg of aluminum particles and 25kg of silicon carbide were used to strengthen deoxidation, the pressure of bottom blowing argon was adjusted to 0.55MPa, and the white slag was realize...
Embodiment 3
[0034] High aluminum nitride steel is produced by the process route of EAF-CONVERTER electric converter smelting→LF furnace refining→VD vacuum treatment→CCM continuous casting:
[0035] The total charge of the electric converter is controlled at 101.81 tons, the molten iron ratio is 95%, the pig iron addition is 2.6 tons, and the rest is high-quality steel scrap. Tapping end point composition C: 0.13%, P: 0.008%, tapping temperature T: 1646°C, tapping volume 85.7 tons; adding 150kg of Al block and 100kg of calcium carbide for deoxidation, adding 445kg of silicon manganese and 2140kg of high carbon ferrochrome and 250kg of ferromolybdenum for post-furnace alloying, and 700kg of lime and 100kg of low-silicon synthetic slag for slagging;
[0036] In the early stage of LF refining, 85kg of aluminum particles and 35kg of silicon carbide were used to strengthen deoxidation, the pressure of bottom blowing argon gas was adjusted to 0.52MPa, and 100kg of lime was added. After 10 minute...
PUM
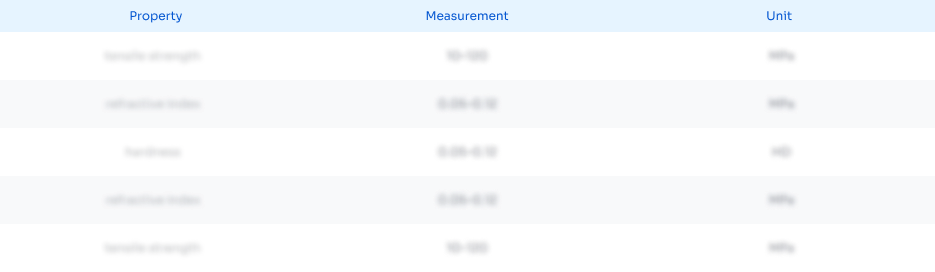
Abstract
Description
Claims
Application Information

- R&D
- Intellectual Property
- Life Sciences
- Materials
- Tech Scout
- Unparalleled Data Quality
- Higher Quality Content
- 60% Fewer Hallucinations
Browse by: Latest US Patents, China's latest patents, Technical Efficacy Thesaurus, Application Domain, Technology Topic, Popular Technical Reports.
© 2025 PatSnap. All rights reserved.Legal|Privacy policy|Modern Slavery Act Transparency Statement|Sitemap|About US| Contact US: help@patsnap.com