A Cement Kiln Bypass Bleeding Combined Staged Combustion Kiln Tail Flue Gas Treatment Device and Process Method
A technology of bypass ventilation and staged combustion, which is applied in the direction of combustion method, waste heat treatment, combustion type, etc., can solve the problems that the staged combustion technology needs to be improved, and achieve the effect of reducing cycle enrichment, reducing emissions, and reducing heat loss
- Summary
- Abstract
- Description
- Claims
- Application Information
AI Technical Summary
Problems solved by technology
Method used
Image
Examples
Embodiment Construction
[0034] Below in conjunction with accompanying drawing and embodiment the present invention is described in further detail:
[0035] like figure 1 As shown, a cement kiln bypass air discharge combined with staged combustion kiln tail flue gas treatment process, under the action of the exhaust fan 15, through the electric bypass air release valve 4 from the connection part of the rotary kiln 1 and the calciner 3, that is, the kiln tail 1% to 15% of the kiln tail flue gas is extracted from the flue chamber 2 as bypass flue gas. The bypass flue gas is fully mixed with the part of the hot raw meal separated from the cyclone preheater C5 through the high-temperature material distribution lock valve 20 in the ascending flue gas pipeline, and the gas-material heat exchange is performed.
[0036] After heat exchange, the flue gas passes through the double cyclone separator 5 to separate 90% of the hot raw material and then enters the bottom of the layered cooling desulfurization tower...
PUM
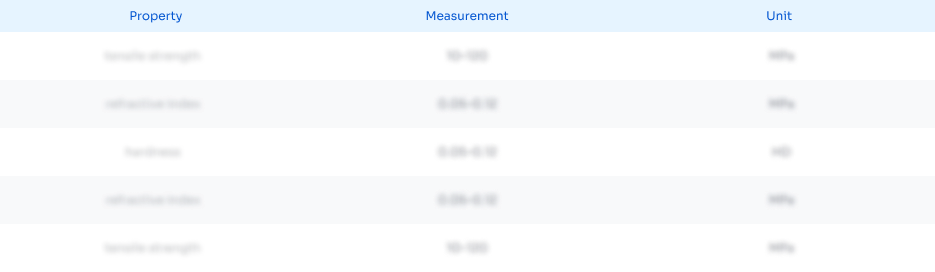
Abstract
Description
Claims
Application Information

- Generate Ideas
- Intellectual Property
- Life Sciences
- Materials
- Tech Scout
- Unparalleled Data Quality
- Higher Quality Content
- 60% Fewer Hallucinations
Browse by: Latest US Patents, China's latest patents, Technical Efficacy Thesaurus, Application Domain, Technology Topic, Popular Technical Reports.
© 2025 PatSnap. All rights reserved.Legal|Privacy policy|Modern Slavery Act Transparency Statement|Sitemap|About US| Contact US: help@patsnap.com