Process for on-line cleaning to double rotational flow gas burner
A gas burner and double-swirl technology, applied in the boiler field, can solve the problems affecting the safe and stable operation of the boiler, the limitation of the continuous operation time of the boiler, and the easy damage of the gas side swirl sheet, so as to reduce the emission of blast furnace gas, reduce the operation and Maintenance cost and the effect of reducing the number of shutdowns
- Summary
- Abstract
- Description
- Claims
- Application Information
AI Technical Summary
Problems solved by technology
Method used
Image
Examples
Embodiment Construction
[0040] The present invention will be further described below in conjunction with accompanying drawing, but not as limiting the present invention:
[0041]A process for online cleaning of double-swirl gas burners, including a gas branch pipe 1, an incoming branch pipe 2, and a furnace 8. The gas branch pipe 1 and the incoming branch pipe 2 are connected in parallel to the purge circuit main pipe 3, and the purge circuit main pipe 3 It is connected in two ways, one way is connected to the cut-off valve and then connected to the branch pipe 4 of the upper row of burner purge circuit, and the other way is connected to the stop valve and then connected to the branch pipe 11 of the lower row of burner purge circuit; the upper row of burner purge circuit The branch pipe 4 is connected to the cut-off valve and then connected in two ways, one of which is connected to the branch pipe 5 of the right half swirl sheet purge circuit of the burner, and the other end of the branch pipe 5 of th...
PUM
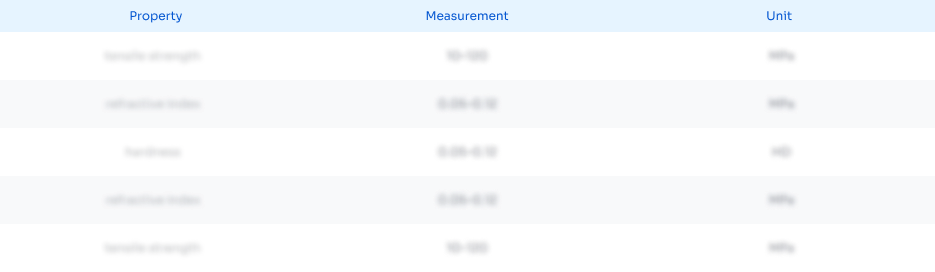
Abstract
Description
Claims
Application Information

- Generate Ideas
- Intellectual Property
- Life Sciences
- Materials
- Tech Scout
- Unparalleled Data Quality
- Higher Quality Content
- 60% Fewer Hallucinations
Browse by: Latest US Patents, China's latest patents, Technical Efficacy Thesaurus, Application Domain, Technology Topic, Popular Technical Reports.
© 2025 PatSnap. All rights reserved.Legal|Privacy policy|Modern Slavery Act Transparency Statement|Sitemap|About US| Contact US: help@patsnap.com