Hybridization wall material nano-capsules made of phase change energy storage material and preparation method of hybridization wall material nano-capsules
A phase change energy storage material and nanocapsule technology, which is applied in the field of hybrid wall material nanocapsules of phase change energy storage materials and their preparation, can solve the problems of high brittleness and poor mechanical strength, and achieve regular morphology and little influence. , the effect of high yield
- Summary
- Abstract
- Description
- Claims
- Application Information
AI Technical Summary
Problems solved by technology
Method used
Image
Examples
Embodiment 1
[0038] In a 100 mL three-necked flask, add 1.0 g of n-octadecane, 0.75 mL of LTEOS, 0.375 mL of MPS, 0.375 mL of styrene, and 0.015 g of AIBN, and mix to form an oil phase. Thereafter, 28.5 mL of water and 14.2 mL of ethanol were sequentially added into the three-necked flask, and the water and ethanol were miscible as the water phase. Thereafter, 0.246 g of CTAB was added into the three-necked flask, and magnetically stirred at 35° C. for 30 min at a rotational speed of 1500 r / min. Then immediately use an ultrasonic cleaner (KQ-400KDB type, 100% amplitude) to sonicate at 35° C. for 10 min to form a stable miniemulsion. Nitrogen was passed into the three-necked flask for 30 minutes, and then 1.04 mL of ammonia water with a mass concentration of 25 wt % was added. Continue nitrogen protection, put the three-necked flask into an 80°C oil bath, and stir for 4 hours with a magnetic force at a stirring rate of 300r / min. During this process, TEOS and MPS undergo a hydrolysis-conde...
Embodiment 2
[0040] In a 1000mL beaker, add 10g of n-octadecane, 7.5mLTEOS, 3.75mL of MPS, 3.75mL of styrene, and 0.15g of AIBN to form an oil phase after miscibility. Thereafter, 285 mL of water and 142 mL of ethanol were added to the beaker successively, and the water and ethanol were miscible as the water phase. Thereafter, 2.46 g of CTAB was added into the beaker, and emulsified at 35° C. under high-speed shear (UltraTurrax T25 type, 10000 r / min) for 2 min. Then immediately use a sonicator (VCX-750 type, 40% amplitude) to sonicate at 35° C. for 10 min to form a stable miniemulsion. Pour the miniemulsion into a 500 mL three-necked bottle, pass nitrogen gas inside for 30 minutes, and then add 10.4 mL of ammonia water with a mass concentration of 25 wt%. The three-neck flask was continuously ventilated with nitrogen, and placed in an oil bath at 80°C, and magnetically stirred for 4 hours at a stirring rate of 300 r / min. During this process, TEOS and MPS undergo a hydrolysis-condensation...
Embodiment 3
[0042] In a 1000mL beaker, add 10g of n-butyl stearate, 10mL of vinyltrimethoxysilane, 5mL of methyl methacrylate, and 0.15g of tert-butyl hydroperoxide to form an oil phase after miscibility. Thereafter, 320 mL of water and 107 mL of ethanol were successively added into the beaker, and the water and ethanol were miscible as the water phase. Thereafter, 2.00 g of sodium lauryl sulfate was added into the beaker, and emulsified at 35°C for 2 min at high-speed shear (UltraTurrax T25 type, 10000 r / min). Then immediately use a sonicator (VCX-750 type, 40% amplitude) to sonicate at 35° C. for 10 min to form a stable miniemulsion. Pour the miniemulsion into a 500mL three-neck bottle, pass nitrogen gas inside for 30min, and then add 2.0mL of sodium hydroxide solution with a mass concentration of 5wt%. The three-neck flask was continuously ventilated with nitrogen, and placed in an oil bath at 80°C, and magnetically stirred for 3 hours at a stirring rate of 300 r / min. The reacted mix...
PUM
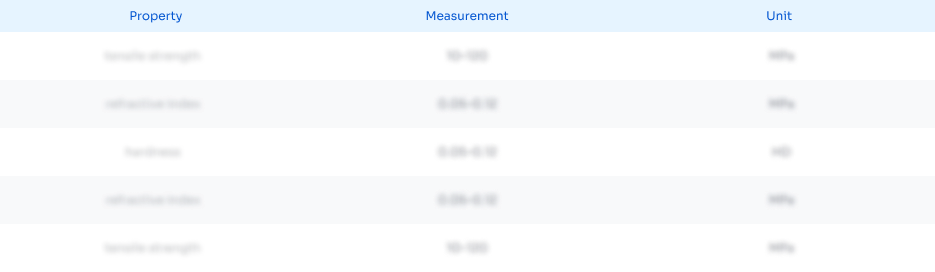
Abstract
Description
Claims
Application Information

- R&D Engineer
- R&D Manager
- IP Professional
- Industry Leading Data Capabilities
- Powerful AI technology
- Patent DNA Extraction
Browse by: Latest US Patents, China's latest patents, Technical Efficacy Thesaurus, Application Domain, Technology Topic, Popular Technical Reports.
© 2024 PatSnap. All rights reserved.Legal|Privacy policy|Modern Slavery Act Transparency Statement|Sitemap|About US| Contact US: help@patsnap.com