A double-station robot automatic welding production line for milling drum tool holders
An automatic welding and robot technology, applied in welding equipment, welding equipment, auxiliary welding equipment, etc., can solve the problems of increased vibration of the whole machine, high labor intensity of workers, poor consistency of welding quality, etc., to improve the degree of automation and labor intensity of workers. Low, high welding consistency effect
- Summary
- Abstract
- Description
- Claims
- Application Information
AI Technical Summary
Problems solved by technology
Method used
Image
Examples
Embodiment Construction
[0018] The present invention will be further described below in conjunction with drawings and embodiments.
[0019] as attached figure 1 , attached figure 2 And attached image 3 As shown, the present invention comprises a spot welding station, a full welding station and a material transfer device. The spot welding station and a full welding station are respectively arranged at two ends of the material transfer device, and the material transfer device moves between the spot welding station and the full welding station. between welders. After the milling drum completes the spot welding process of the tool holder at the spot welding station, it is transported by the material transfer device to the full welding station for full welding processing.
[0020] The material transfer device includes two guide rails 7, a mobile slide 3, a set of roller supports 5, a set of single-axis positioner 4 and a set of driving motor; the drive motor is fixed on the mobile slide 3, and the dr...
PUM
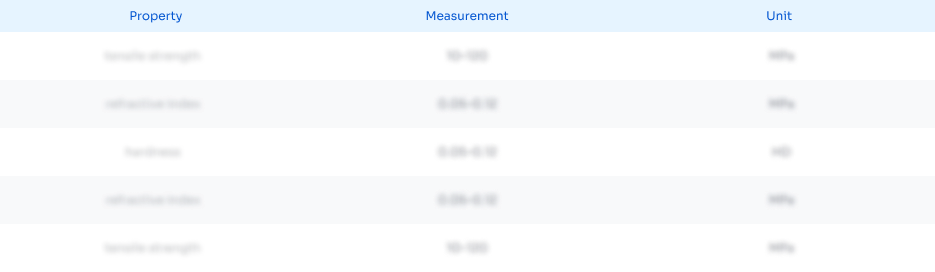
Abstract
Description
Claims
Application Information

- R&D
- Intellectual Property
- Life Sciences
- Materials
- Tech Scout
- Unparalleled Data Quality
- Higher Quality Content
- 60% Fewer Hallucinations
Browse by: Latest US Patents, China's latest patents, Technical Efficacy Thesaurus, Application Domain, Technology Topic, Popular Technical Reports.
© 2025 PatSnap. All rights reserved.Legal|Privacy policy|Modern Slavery Act Transparency Statement|Sitemap|About US| Contact US: help@patsnap.com