Production technology of spring steel alloy
A production process and spring steel technology, applied in the field of steel alloys, can solve the problems of increased heat treatment costs, decreased plasticity and toughness, personal injury, etc., and achieve the effect of reducing crack growth rate, reducing formation and spreading, and improving corrosion resistance.
- Summary
- Abstract
- Description
- Claims
- Application Information
AI Technical Summary
Problems solved by technology
Method used
Examples
Embodiment 1
[0051] S1. Weigh C0.42%, Si1.69%, Mn0.18%, P0.004%, S0.007%, Cu0.2%, Ni0.33%, Cr1.16%, V0.05%, Ti0 .5%, Al0.027% and unavoidable impurities are put into a vacuum smelting furnace for smelting, and then heated and forged to obtain a spring steel alloy billet;
[0052] S2, placing the spring steel alloy parison obtained in step S1 on the drilling machine and the rolling earphone to perform drilling and ear rolling operations to obtain the spring steel alloy profile;
[0053] S3, performing a quenching process on the spring steel alloy profile obtained in step S2 to obtain a spring steel alloy material, and performing an oil cooling operation after quenching;
[0054] S4, subjecting the spring steel alloy material obtained in step S3 to a medium temperature tempering treatment, performing a shot peening process after the medium temperature tempering treatment, and then performing a pre-pressing operation to obtain a spring steel alloy primary product;
[0055] S5. After annealin...
Embodiment 2
[0063] S1. Weigh C0.5%, Si1.70%, Mn0.10%, P0.004%, S0.008%, Cu0.21%, Ni0.41%, Cr1.22%, V0.12%, Ti0 .55%, Al0.027% and unavoidable impurities are put into a vacuum smelting furnace for smelting, and then heated and forged to obtain a spring steel alloy billet;
[0064] S2, placing the spring steel alloy parison obtained in step S1 on the drilling machine and the rolling earphone to perform drilling and ear rolling operations to obtain the spring steel alloy profile;
[0065] S3, performing a quenching process on the spring steel alloy profile obtained in step S2 to obtain a spring steel alloy material, and performing an oil cooling operation after quenching;
[0066] S4, subjecting the spring steel alloy material obtained in step S3 to a medium temperature tempering treatment, performing a shot peening process after the medium temperature tempering treatment, and then performing a pre-pressing operation to obtain a spring steel alloy primary product;
[0067] S5. After anneali...
Embodiment 3
[0075] S1. Weigh C0.35%, Si1.10%, Mn0.10%, P0.004%, S0.005%, Cu0.18%, Ni0.28%, Cr1.09%, V0.04%, Ti0 .4%, Al0.027% and unavoidable impurities are put into a vacuum smelting furnace for smelting, and then heated and forged to obtain a spring steel alloy billet;
[0076] S2, placing the spring steel alloy parison obtained in step S1 on the drilling machine and the rolling earphone to perform drilling and ear rolling operations to obtain the spring steel alloy profile;
[0077] S3, performing a quenching process on the spring steel alloy profile obtained in step S2 to obtain a spring steel alloy material, and performing an oil cooling operation after quenching;
[0078] S4, subjecting the spring steel alloy material obtained in step S3 to a medium temperature tempering treatment, performing a shot peening process after the medium temperature tempering treatment, and then performing a pre-pressing operation to obtain a spring steel alloy primary product;
[0079] S5. After anneali...
PUM
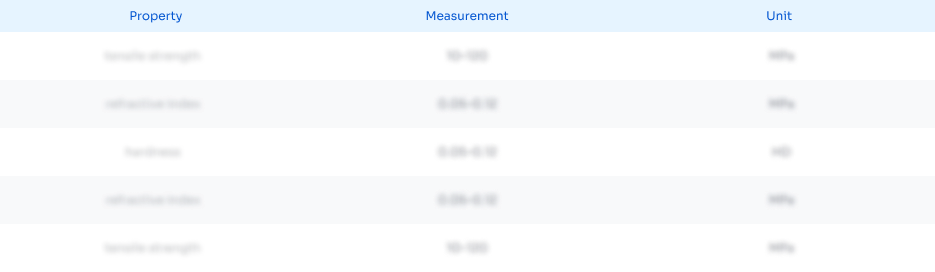
Abstract
Description
Claims
Application Information

- R&D
- Intellectual Property
- Life Sciences
- Materials
- Tech Scout
- Unparalleled Data Quality
- Higher Quality Content
- 60% Fewer Hallucinations
Browse by: Latest US Patents, China's latest patents, Technical Efficacy Thesaurus, Application Domain, Technology Topic, Popular Technical Reports.
© 2025 PatSnap. All rights reserved.Legal|Privacy policy|Modern Slavery Act Transparency Statement|Sitemap|About US| Contact US: help@patsnap.com