A coating control method and its application
A control method and coating technology, which is applied in coating, hot-dip coating process, metal material coating process, etc., can solve the problems of difficult coating, limited production line speed, and deteriorated surface quality, etc., to achieve low cost and lift plate The effect of improving surface quality and breaking through the bottleneck of production speed
- Summary
- Abstract
- Description
- Claims
- Application Information
AI Technical Summary
Problems solved by technology
Method used
Image
Examples
Embodiment Construction
[0040] The implementation of the present invention will be illustrated by specific specific examples below, and those skilled in the art can easily understand other advantages and effects of the present invention from the contents disclosed in this specification.
[0041] A coating control method applied to hot-dip galvanizing (GI and GA), hot-dip galvanized silicon (55% Al-Zn-Si), hot-dip galvanized aluminum-silicon (5% Al-Zn-Si), hot-dip aluminum Zinc-magnesium, hot-dip aluminum-silicon and other hot-dip fields.
[0042]The main points are: in the process of hot-dip plating, when the strip steel leaves the liquid surface of the plating solution, the ultrasonic wave is first used to carry out ultrasonic vibration treatment on the plating solution brought out of the liquid surface of the strip steel. The vibration generated by the ultrasonic wave in the metal liquid will make the viscous The metal liquid attached to the surface of the strip produces a splash effect, and part o...
PUM
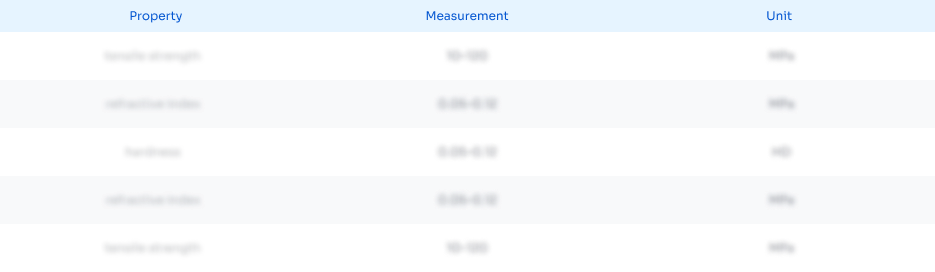
Abstract
Description
Claims
Application Information

- R&D Engineer
- R&D Manager
- IP Professional
- Industry Leading Data Capabilities
- Powerful AI technology
- Patent DNA Extraction
Browse by: Latest US Patents, China's latest patents, Technical Efficacy Thesaurus, Application Domain, Technology Topic, Popular Technical Reports.
© 2024 PatSnap. All rights reserved.Legal|Privacy policy|Modern Slavery Act Transparency Statement|Sitemap|About US| Contact US: help@patsnap.com