Method for applying fluctuating pressure in low-pressure casting process
A low-pressure casting and pressure technology, which is applied in the field of special forming of non-ferrous alloys, can solve problems such as shrinkage cavities and porosity, and achieve the effects of improving feeding capacity, promoting feeding range, and eliminating shrinkage cavities and porosity defects
- Summary
- Abstract
- Description
- Claims
- Application Information
AI Technical Summary
Problems solved by technology
Method used
Image
Examples
specific Embodiment approach 1
[0011] Specific implementation mode 1: The method for applying fluctuating pressure in the low pressure casting process of this embodiment is carried out according to the following steps:
[0012] When low-pressure casting is performed on alloy castings, when the alloy castings complete the lifting phase, filling phase, and pressurization phase, enter the pressure holding phase to apply fluctuating pressure to maintain the pressure. After the pressure is maintained until the casting is completely solidified, the fluctuating pressure is unloaded to complete the low pressure Casting.
[0013] The fluctuating pressure described in this embodiment controls the pressure during the holding and solidification period by controlling the pressure increase valve and the pressure relief valve.
specific Embodiment approach 2
[0014] Specific embodiment two: this embodiment is different from specific embodiment one in that: the method of applying fluctuating pressure is: the frequency f of applying fluctuating pressure is 1Hz-50Hz, and the fluctuating pressure range of the pressure holding stage is p~y, so The p is the lower limit of the fluctuating pressure, which is the filling pressure at the end of the filling, and the p is calculated according to the formula p=Hρgμ, where H is from the liquid level in the crucible in the sealed pot after pouring to the highest point of the mold cavity of vertical Height, ρ is the density of alloy liquid, and the unit of ρ is kg / m 3 , Μ is the drag coefficient, g is the acceleration of gravity; the y is the upper limit of the fluctuating pressure, and its value is 0.05 MPa ~ 0.3 MPa. The upper and lower limits of the control fluctuating pressure remain unchanged, and the fluctuating pressure is applied until the end of the pressure holding stage, and the fluctua...
specific Embodiment approach 3
[0015] Specific embodiment three: This embodiment is different from specific embodiment one or two in that the method of applying fluctuating pressure is: the frequency f of applying fluctuating pressure is 1Hz-50Hz, and the fluctuating pressure range of the pressure holding stage is p~y ; The p is the lower limit of the fluctuating pressure, which is the filling pressure at the end of the filling, the p is calculated according to the formula p=Hρgμ, where H is from the liquid level in the crucible in the sealed tank to the mold cavity after pouring The vertical height of the highest point, ρ is the density of the alloy liquid, and the unit of ρ is kg / m 3 , Μ is the drag coefficient, g is the acceleration of gravity; the y is the upper limit of the fluctuating pressure, and its value is 0.05 MPa ~ 0.3 MPa; then the upper and lower limits of the applied fluctuating pressure are controlled, and as the number of cycles n increases, the fluctuating pressure The difference between th...
PUM
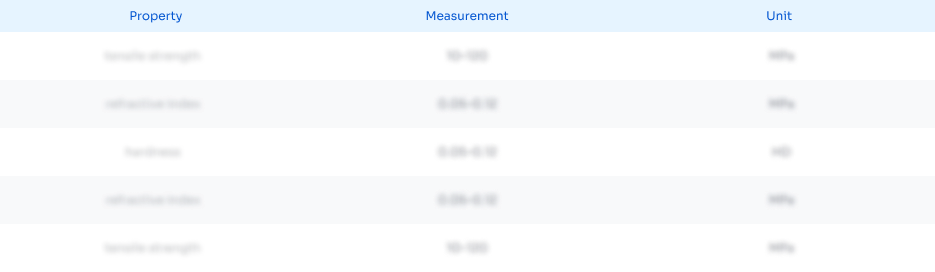
Abstract
Description
Claims
Application Information

- R&D
- Intellectual Property
- Life Sciences
- Materials
- Tech Scout
- Unparalleled Data Quality
- Higher Quality Content
- 60% Fewer Hallucinations
Browse by: Latest US Patents, China's latest patents, Technical Efficacy Thesaurus, Application Domain, Technology Topic, Popular Technical Reports.
© 2025 PatSnap. All rights reserved.Legal|Privacy policy|Modern Slavery Act Transparency Statement|Sitemap|About US| Contact US: help@patsnap.com