Method for calibrating flatness of X-Y plane of microscopic scanning platform
A scanning platform and calibration method technology, applied in microscopes, optics, instruments, etc., can solve problems such as increased hardware complexity, out-of-focus, and increased cost expenditures, and achieve the goal of reducing improvement costs, reducing manufacturing costs, and improving continuous scanning performance Effect
- Summary
- Abstract
- Description
- Claims
- Application Information
AI Technical Summary
Problems solved by technology
Method used
Image
Examples
Embodiment
[0096] The following embodiments describe the calibration method of the microscopic scanning platform in detail. In this embodiment, the moving area of the scanning platform is 100mm * 75mm=7500mm 2 The detailed process steps of its calibration are as follows:
[0097] first step, such as figure 2 As shown in steps 201 and 202, determine the magnification of the microscope lens, the target surface S of the camera imaging chip, and the lens magnification X of the microscope, so as to calculate the physical area S on the XY platform corresponding to the camera imaging photo.
[0098] The second step, such as figure 2 As shown in step 203, calculate the moving area S of the scanning platform, that is, S=100mm×75mm=7500mm 2 , set the camera image size to cover the entire motion area, and calculate the number N of photos required to capture the complete motion area, then N=7500.
[0099] The third step is to determine the XY axis coordinates of each photo taken. If the actua...
PUM
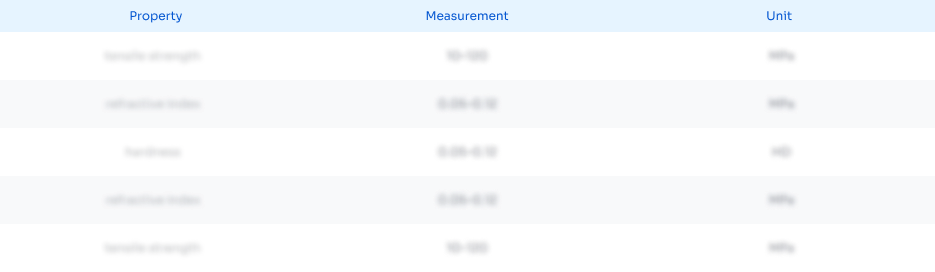
Abstract
Description
Claims
Application Information

- R&D
- Intellectual Property
- Life Sciences
- Materials
- Tech Scout
- Unparalleled Data Quality
- Higher Quality Content
- 60% Fewer Hallucinations
Browse by: Latest US Patents, China's latest patents, Technical Efficacy Thesaurus, Application Domain, Technology Topic, Popular Technical Reports.
© 2025 PatSnap. All rights reserved.Legal|Privacy policy|Modern Slavery Act Transparency Statement|Sitemap|About US| Contact US: help@patsnap.com