Method for coprocessing zinc-contained leaching residues through steel mill dezincification furnace
A technology for zinc leaching slag and steel mills, which is applied in the field of co-processing zinc-containing leaching slag in steel plant dezincification furnaces. It can solve problems such as lack of zinc leaching slag treatment equipment, pollution of zinc-containing leaching slag, and processing capacity can not keep up. The value of resource utilization and the economic benefits of the enterprise, the effect of reducing equipment investment and expanding the scope of use
- Summary
- Abstract
- Description
- Claims
- Application Information
AI Technical Summary
Problems solved by technology
Method used
Examples
Embodiment 1
[0030] The main components of the zinc-containing leaching slag used in this example are shown in Table 1. The smelting equipment for co-processing zinc-containing leaching slag is a steel mill dust rotary kiln with a length of 36m and an inner diameter of 1.8m, and a steel mill dust treatment capacity of 50,000 tons per year. The main components of blast furnace dust as the main raw material are shown in Table 2. The smelting reducing agent adopts third-grade coke powder, and its main components are shown in Table 3.
[0031] Table 1 Main components of zinc-containing leaching slag (dry basis) (wt%)
[0032] Zn
Pb
S
Fe
SiO 2
Al 2 o 3
10.5
6.7
12.7
13.5
18.3
3.4
[0033] Table 2 Main components of blast furnace dust (wt%)
[0034] TF
CaO
SiO 2
MgO
Al 2 o 3
C
Pb
Zn
S
35.2
6.1
12.0
4.2
1.9
16.3
0.35
4.52
0.58
[003...
Embodiment 2
[0045]Co-processing of zinc-containing leach slag in a dusty rotary hearth furnace of a steel mill. The middle diameter of the rotary hearth furnace used is 21m; the inner width of the furnace is 5m, and the dust handling capacity is 200,000 tons / year. The main components of zinc leaching slag are shown in Table 1, and the main components of steel mill dust are shown in Table 4. The reducing agent is anthracite, with a calorific value of 5500kCal / kg and a fixed carbon content of 73%.
[0046] Table 4 Main components of steel mill dust (wt%)
[0047] TF
C
SiO 2
CaO
MgO
Al 2 o 3
Zn
Pb
S
51.2
5.8
2.3
11.2
1.7
0.8
0.52
0.12
0.32
[0048] The smelting steps are as follows:
[0049] The first step: the used zinc-containing leaching slag and coke powder are mixed into the steel mill dust, wherein the amount of zinc-containing leaching slag added accounts for 2.0% of the quality of the steel...
PUM
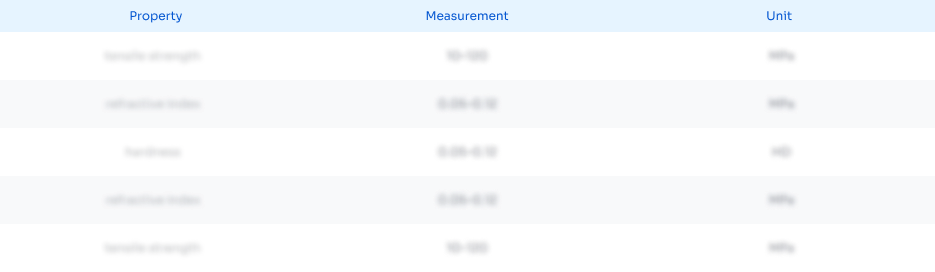
Abstract
Description
Claims
Application Information

- Generate Ideas
- Intellectual Property
- Life Sciences
- Materials
- Tech Scout
- Unparalleled Data Quality
- Higher Quality Content
- 60% Fewer Hallucinations
Browse by: Latest US Patents, China's latest patents, Technical Efficacy Thesaurus, Application Domain, Technology Topic, Popular Technical Reports.
© 2025 PatSnap. All rights reserved.Legal|Privacy policy|Modern Slavery Act Transparency Statement|Sitemap|About US| Contact US: help@patsnap.com