Preparation method of single side oxidized cellulose film
A cellulose film and single-sided oxidation technology, which is applied in the field of preparation of single-sided oxidized cellulose film, can solve the problems of cellulose film waste and application restrictions, and achieve the effects of high reaction efficiency, simple operation, and low dosage
- Summary
- Abstract
- Description
- Claims
- Application Information
AI Technical Summary
Problems solved by technology
Method used
Image
Examples
Embodiment 1
[0021] (1) Preparation of cellulose film: disperse the cotton linters in the alkaline solution, freeze the resulting cellulose suspension at low temperature, take it out after 24 hours, stir it with high-speed machinery, and centrifuge. The cellulose solution obtained by this simple method is placed in a glass Push the plate to make a thin layer, then immerse in concentrated sulfuric acid solution to solidify and regenerate to obtain a transparent cellulose film, and the cellulose film is washed repeatedly with deionized water before use.
[0022] (2) Buffer solution configuration: 3.3-3.6g of boric acid is dissolved in 800ml of water, diluted with 0.1mol / L sodium hydroxide solution, so that the pH of the solution is 10-11
[0023] (3) Impregnation of cellulose membrane: Dissolve 2 g of sodium bromide and 0.3 g of TEMPO reagent in the buffer solution configured in (2) above, and after mixing evenly with magnetic stirring, immerse the cellulose membrane in the configured solutio...
Embodiment 2
[0028] (1) Preparation of cellulose film: at room temperature, immerse bacterial cellulose dried to absolute dryness in 100 mL ethylenediamine solution for 90 min, then wash with a large amount of distilled water and methanol, and dry in vacuum at 80 °C. Add 100mL of DMAc and 8g of LiCl dried in vacuum at 150°C into a 250mL three-neck round bottom flask, then stir, and heat the three-neck flask with an oil bath. After the LiCl was completely dissolved, the bacterial cellulose impregnated with ethylenediamine was added, heated and stirred for 3 hours, cooled to room temperature and left to stand until it was completely dissolved. The above bacterial cellulose solution was scraped on a constant temperature hot glass plate to form a film, immersed in a coagulation bath at 25°C, and then dried naturally.
[0029] (2) Buffer solution configuration: 3.3-3.6g of boric acid is dissolved in 800ml of water, diluted with 0.1mol / L sodium hydroxide solution, so that the pH of the solution ...
Embodiment 3
[0035] (1) Preparation of cellulose film: Dilute the nanocellulose suspension obtained by acid hydrolysis to 0.5 wt%, and treat it with 300W ultrasonic power for 10 minutes in an ice bath to ensure that the nanocellulose is uniformly dispersed in water. Then filter the above-mentioned diluted solution with a glass membrane-changing filter device covered with an organic filter membrane, and vacuum filter with a vacuum pump. After the nanocellulose is uniformly formed into a nanocellulose membrane, take it out together with the organic filter membrane, cover with an organic filter membrane, dry at room temperature for 2 to 3 days, and then move to a vacuum oven at 60°C to dry for 2 to 3 days. sky. After drying, it is uncovered to obtain a transparent nanocellulose film.
[0036] (2) Buffer solution configuration: 3.3-3.6g boric acid is dissolved in 800ml water, diluted with 0.1mol / L potassium hydroxide solution, so that the pH of the solution is 10-11.
[0037] (3) Impregnatio...
PUM
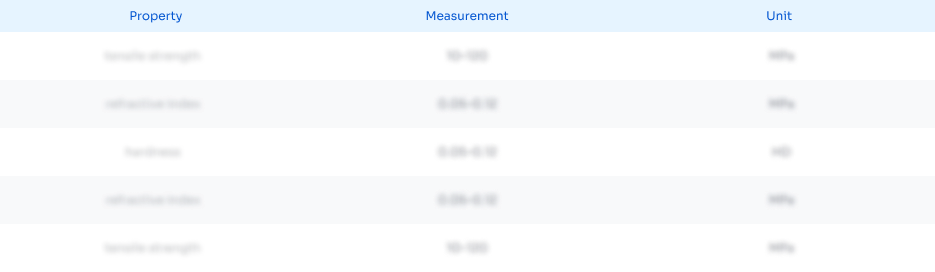
Abstract
Description
Claims
Application Information

- R&D
- Intellectual Property
- Life Sciences
- Materials
- Tech Scout
- Unparalleled Data Quality
- Higher Quality Content
- 60% Fewer Hallucinations
Browse by: Latest US Patents, China's latest patents, Technical Efficacy Thesaurus, Application Domain, Technology Topic, Popular Technical Reports.
© 2025 PatSnap. All rights reserved.Legal|Privacy policy|Modern Slavery Act Transparency Statement|Sitemap|About US| Contact US: help@patsnap.com