Laser cladding and self-adaptive milling integrated combined numerical-control machine tool for repairing blade
A composite CNC machine tool and laser cladding technology, which is applied to other manufacturing equipment/tools, manufacturing tools, etc., can solve the problems of large grinding allowance, hard-to-blade surfacing layer, difficult-to-remove material allowance processing, etc., to achieve Improve processing efficiency and precision, save equipment procurement costs, and facilitate intelligent management and control
- Summary
- Abstract
- Description
- Claims
- Application Information
AI Technical Summary
Problems solved by technology
Method used
Image
Examples
Embodiment Construction
[0033] The present invention will be further described below in conjunction with accompanying drawing. Embodiments of the present invention include, but are not limited to, the following examples.
[0034] Such asfigure 1 , figure 2 , image 3 As shown, it is the front view, side view and A-A view of a preferred example of the laser cladding and adaptive milling integrated CNC machine tool for blade repair of the present invention. It mainly includes installing a first column (26) for realizing milling and a second column (45) for laser cladding surfacing on the double T-shaped bed (10), which is arranged at one end of the bed and driven by a servo motor (38 ) drive the screw rod (47) to drive the sliding workbench to realize the X-direction movement. The rotary table (12) installed on the sliding table is driven by the A-direction servo motor (37) to realize continuous 360° rotary motion, and the blade (2) to be repaired is installed on the fixture (1) arranged on the wor...
PUM
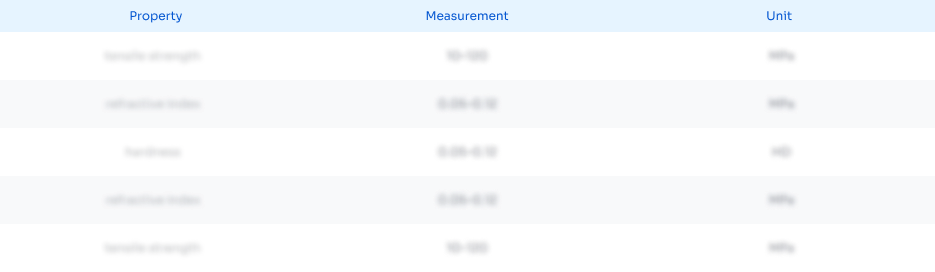
Abstract
Description
Claims
Application Information

- R&D Engineer
- R&D Manager
- IP Professional
- Industry Leading Data Capabilities
- Powerful AI technology
- Patent DNA Extraction
Browse by: Latest US Patents, China's latest patents, Technical Efficacy Thesaurus, Application Domain, Technology Topic, Popular Technical Reports.
© 2024 PatSnap. All rights reserved.Legal|Privacy policy|Modern Slavery Act Transparency Statement|Sitemap|About US| Contact US: help@patsnap.com