A kind of method that prepares graphene by thermal plasticization graphite material
A technology of graphite materials and thermoplastic materials, applied in the field of graphene materials, can solve the problems of difficulty in obtaining graphene, insufficient shear force to overcome van der Waals forces of the graphite layer, and small lateral size of graphene, so as to overcome serious environmental pollution and safety. The effect of avoiding hidden dangers, preserving lattice integrity, and reducing production costs
- Summary
- Abstract
- Description
- Claims
- Application Information
AI Technical Summary
Problems solved by technology
Method used
Image
Examples
Embodiment 1
[0037] 1) Add 85 parts by weight of graphite, 5 parts by weight of hydroxyl-terminated polybutadiene, and 0.5 parts by weight of chain extender 1,2-propylene glycol into a vacuum kneader for kneading, and the temperature of the vacuum kneader rises to 80-100 ℃, under the condition of 50rpm low-speed stirring, kneading and kneading for 20 minutes, the hydroxyl-terminated polybutadiene is inserted into the graphite layer by means of the terminal hydroxyl group to weaken the van der Waals force, and obtain a premix;
[0038] 2) Add the premix obtained in step 1) and 5 parts by weight of polar polymer polymethyl methacrylate to the first-stage main feeding port of the two-stage screw extruder, and the first-stage screw machine is Counter-rotating conical twin-screw extruder, the screw speed is 800rpm, the heating temperature of the screw extruder is controlled at 280°C, the screw extruder is equipped with an auxiliary feeding port, and an initiator is added to oxidize dibenzoyl at ...
Embodiment 2
[0042] 1) 90 parts by weight of graphite, 8 parts by weight of hydroxyl-terminated polybutadiene, and 1 part by weight of chain extender 1,4-butanediol are added to a vacuum kneader for kneading, and the temperature of the vacuum kneader rises to 80 -100°C, under the condition of 60rpm low-speed stirring, kneading and kneading for 25 minutes, the hydroxyl-terminated polybutadiene is inserted into the graphite layer by means of terminal hydroxyl groups to weaken the van der Waals force, and a premix is obtained;
[0043] 2) Add the premix obtained in step 1) and 6 parts by weight of the polar polymer polyethylene terephthalate to the first stage of the two-stage screw extruder, and the first stage screw machine is different To the conical twin-screw extruder, control the heating temperature of the screw extruder at 320°C, set the auxiliary feed port on the screw extruder, add the initiator dicumyl peroxide to the auxiliary feed port, and the initiator triggers the chain extend...
Embodiment 3
[0047] 1) The graphite of 86 parts by weight, the hydroxyl-terminated polybutadiene of 10 parts by weight, the chain extender 1 bisphenol A series diol of 1.5 parts by weight are added into a vacuum kneader and kneaded, and the temperature of the vacuum kneader is raised to 80 -100°C, under the condition of 80rpm low-speed stirring, kneading and kneading for 30 minutes, the hydroxyl-terminated polybutadiene is inserted into the graphite layer by means of the terminal hydroxyl group to weaken the van der Waals force, and a premix is obtained;
[0048] 2) Add the premix obtained in step 1) and 8 parts by weight of polar polymer polycarbonate to the first stage of a two-stage screw extruder, and the first stage screw machine is a counter-rotating conical twin-screw Extruder, control the heating temperature of the screw extruder at 280°C, set the auxiliary feeding port on the screw extruder, add the initiator azobisisobutyronitrile to the auxiliary feeding port, and the initiator...
PUM
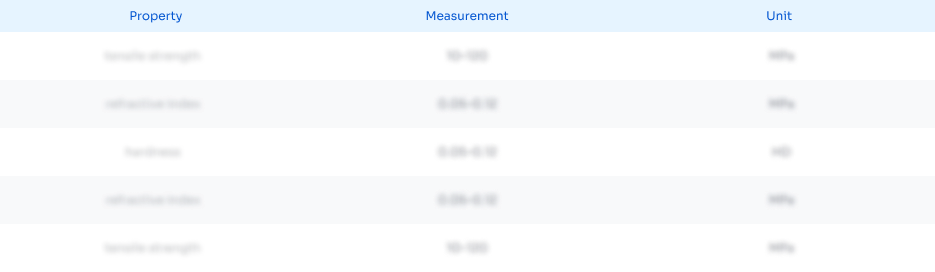
Abstract
Description
Claims
Application Information

- R&D Engineer
- R&D Manager
- IP Professional
- Industry Leading Data Capabilities
- Powerful AI technology
- Patent DNA Extraction
Browse by: Latest US Patents, China's latest patents, Technical Efficacy Thesaurus, Application Domain, Technology Topic, Popular Technical Reports.
© 2024 PatSnap. All rights reserved.Legal|Privacy policy|Modern Slavery Act Transparency Statement|Sitemap|About US| Contact US: help@patsnap.com