Chlorinated butyl rubber and silicone rubber blended material
A technology of chlorinated butyl rubber and silicone rubber, which is applied in the field of chemical materials and can solve the problems of large skin irritation, easy deformation, and poor air tightness
- Summary
- Abstract
- Description
- Claims
- Application Information
AI Technical Summary
Problems solved by technology
Method used
Image
Examples
Embodiment 1
[0038] Chlorobutyl rubber and silicone rubber blend materials, comprising the following components by weight:
[0039] Chlorobutyl rubber 85 parts,
[0040] 12 parts of silicone rubber,
[0041] Zhongchao wear-resistant carbon black n22045 parts,
[0042] High wear-resistant carbon black n33030 parts,
[0043] 10 parts of zinc oxide,
[0044] 6 parts of magnesium oxide,
[0045] Accelerator TT5 parts,
[0046] Accelerator ZDC8 parts,
[0047] Vulcanizing agent DCP5 parts,
[0048] 6 parts of stearic acid,
[0049] Antioxidant methylidene 442610 parts,
[0050] Anti-aging agent MB6 parts.
[0051] The mixing process of mixed materials is as follows:
[0052] XK-160mm open rubber mixing machine is used for mixing rubber materials, and the speed ratio of the rollers is 1:1.25. When mixing chlorinated butyl rubber, the temperature of the front roll should be 50-55°C, and the temperature of the rear roll should be slightly higher, preferably 60-62°C. The mixing process ...
Embodiment 2
[0061] Chlorobutyl rubber and silicone rubber blend materials, comprising the following components by weight:
[0062] Chlorobutyl rubber 80 parts,
[0063] 10 parts of silicone rubber,
[0064] Zhongchao wear-resistant carbon black n22030 parts,
[0065] High wear-resistant carbon black n33010 parts,
[0066] 12 parts of zinc oxide,
[0067] Magnesium oxide 1 part,
[0068] Accelerator TT0 part,
[0069] Accelerator ZDC 2 parts,
[0070] Vulcanizing agent DCP6 parts,
[0071] 8 parts of stearic acid,
[0072] Antioxidant methylidene 442612 parts,
[0073] 2 copies of antioxidant MB.
[0074] The preparation method of the blended material is the same as in Example 1.
Embodiment 3
[0076] Chlorobutyl rubber and silicone rubber blend materials, comprising the following components by weight:
[0077] Chlorobutyl rubber 70 parts,
[0078] 5 parts of silicone rubber,
[0079] Zhongchao wear-resistant carbon black n22040 parts,
[0080] High wear-resistant carbon black n33025 parts,
[0081] Zinc oxide 5 parts,
[0082] 8 parts of magnesium oxide,
[0083] Accelerator TT4 parts,
[0084] Accelerator ZDC5 parts,
[0085] Vulcanizing agent DCP8 parts,
[0086] 4 parts stearic acid,
[0087] 44262 parts of antioxidant methylidene,
[0088] Anti-aging agent MB7 parts.
[0089] The preparation method of the blended material is the same as in Example 1.
PUM
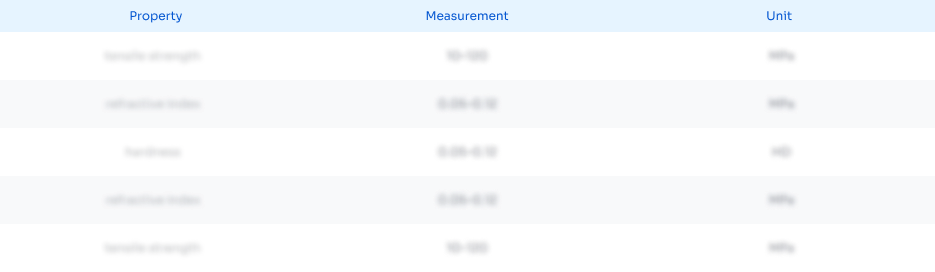
Abstract
Description
Claims
Application Information

- R&D Engineer
- R&D Manager
- IP Professional
- Industry Leading Data Capabilities
- Powerful AI technology
- Patent DNA Extraction
Browse by: Latest US Patents, China's latest patents, Technical Efficacy Thesaurus, Application Domain, Technology Topic, Popular Technical Reports.
© 2024 PatSnap. All rights reserved.Legal|Privacy policy|Modern Slavery Act Transparency Statement|Sitemap|About US| Contact US: help@patsnap.com