Lead-free tin-soldering wire applied to automatic soldering robot and preparation method thereof
An automatic soldering and lead-free soldering technology, applied in the preparation of lead-free solder wire, in the field of lead-free solder wire, can solve problems such as sharpening, tin connection, tin beading, etc., and achieve high expansion rate, good soldering effect, and wetting good sex effect
- Summary
- Abstract
- Description
- Claims
- Application Information
AI Technical Summary
Problems solved by technology
Method used
Examples
Embodiment 1
[0022] Put Cu0.3kg and Sn19.7kg into a high-temperature furnace, fully fuse in a high-temperature furnace at 850 °C, stir for 5 minutes, and keep warm for 15 minutes to prepare a Sn-Cu alloy. Take Ge0.1kg and Sn19.9kg and put them into a high-temperature furnace. Fully fused in a high-temperature furnace at 1400°C, stirred for 8 minutes, and kept warm for 16 minutes to prepare a Sn‐Ge alloy. Take Ni0.07kg and Sn19.93kg and put them into a high-temperature furnace, fully fuse in a high-temperature furnace at 1400°C, stir for 10 minutes, and hold for 18 minutes Finally, the Sn-Ni alloy was obtained, and P0.01kg and Sn19.99kg were put into a high-temperature furnace, fully fused in a high-temperature furnace at 800°C, stirred for 8 minutes, and kept for 20 minutes to obtain a Sn-P alloy, and Nd0.01kg, Sn19 .99kg into the high-temperature furnace, fully fused in the high-temperature furnace at 1250°C, stirred for 8 minutes, and kept for 20 minutes to obtain a Sn-Nd alloy.
[0023]...
Embodiment 2
[0025] Put Cu0.5kg and Sn19.5kg into a high-temperature furnace, fully fuse in a high-temperature furnace at 850°C, stir for 5 minutes, and keep warm for 18 minutes to prepare a Sn‐Cu alloy. Take Ge0.2kg and Sn19.8kg and put them into a high-temperature furnace, ℃ high-temperature furnace fully fused, stirred for 5 minutes, and kept warm for 15 minutes to prepare a Sn-Ge alloy. Take Ni0.03kg and Sn19.97kg into the high-temperature furnace, fully fuse in a 1400℃ high-temperature furnace, stir for 10 minutes, and keep warm for 20 minutes Finally, the Sn-Ni alloy was obtained, and P0.006kg and Sn19.994kg were put into a high-temperature furnace, fully fused in a high-temperature furnace at 800°C, stirred for 10 minutes, and kept for 15 minutes to obtain a Sn-P alloy, and Nd0.02kg, Sn19 .98kg was put into a high-temperature furnace, fully fused in a high-temperature furnace at 1250°C, stirred for 8 minutes, and kept for 20 minutes to obtain a Sn-Nd alloy.
[0026] Heat the Sn-Cu a...
Embodiment 3
[0028] Put Cu0.8kg and Sn19.2kg into a high-temperature furnace, fully fuse in a high-temperature furnace at 850°C, stir for 8 minutes, and keep warm for 18 minutes to prepare a Sn-Cu alloy. Take Ge0.16kg and Sn19.84kg and put them into a high-temperature furnace. Fully fused in a high-temperature furnace at 1400°C, stirred for 10 minutes, and kept warm for 15 minutes to prepare a Sn‐Ge alloy. Take Ni0.05kg and Sn19.95kg and put them into a high-temperature furnace, fully fuse in a high-temperature furnace at 1400°C, stir for 10 minutes, and hold for 18 minutes Finally, the Sn-Ni alloy was obtained, and P0.004kg and Sn19.996kg were put into a high-temperature furnace, fully fused in a high-temperature furnace at 800°C, stirred for 5 minutes, and kept for 20 minutes to obtain a Sn-P alloy, and Nd0.03kg, Sn19 .97kg was put into a high-temperature furnace, fully fused in a high-temperature furnace at 1250°C, stirred for 10 minutes, and kept for 15 minutes to obtain a Sn-Nd alloy. ...
PUM
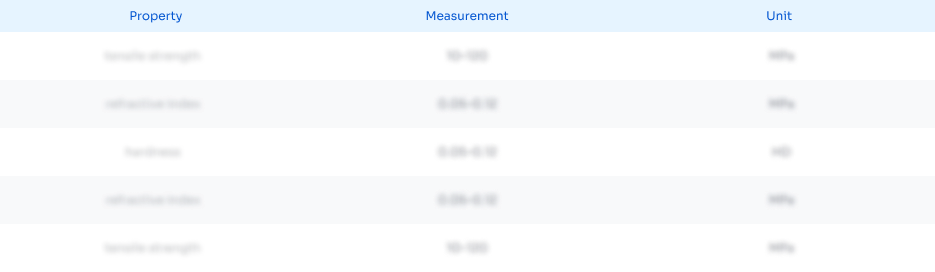
Abstract
Description
Claims
Application Information

- R&D
- Intellectual Property
- Life Sciences
- Materials
- Tech Scout
- Unparalleled Data Quality
- Higher Quality Content
- 60% Fewer Hallucinations
Browse by: Latest US Patents, China's latest patents, Technical Efficacy Thesaurus, Application Domain, Technology Topic, Popular Technical Reports.
© 2025 PatSnap. All rights reserved.Legal|Privacy policy|Modern Slavery Act Transparency Statement|Sitemap|About US| Contact US: help@patsnap.com