Method for manufacturing automotive oil conveying pipe
A production method and technology of oil pipelines, which are applied in the field of automobile oil pipelines, can solve the problems of high temperature aging resistance, personal safety hazards, damage, etc., and achieve the effects of good fuel resistance, simple production process, and wide temperature range
- Summary
- Abstract
- Description
- Claims
- Application Information
AI Technical Summary
Problems solved by technology
Method used
Examples
Embodiment Construction
[0015] The following describes the embodiments of the present invention in detail.
[0016] The present invention provides a method for manufacturing an automobile oil pipeline. The automobile oil pipeline includes an inner pipe and an outer pipe, and includes the following steps:
[0017] A. The inner tube rubber component and the outer tube rubber component are respectively sent to the internal mixer for mixing, using the rotor speed of 10RPM ~ 30RPM, and the inlet temperature of the cooling water is controlled at 10 ℃ ~ 20 ℃, after mixing The glue temperature is 100℃~110℃;
[0018] B. Carry out a quick inspection test on the inner tube rubber compound and the outer tube rubber compound after mixing, and specify the index parameters to control the Mooney viscosity and scorch time of the rubber compound, so as to facilitate the extrusion process in the subsequent process;
[0019] C. Put the inner tube rubber compound and the outer tube rubber compound after the quick inspec...
PUM
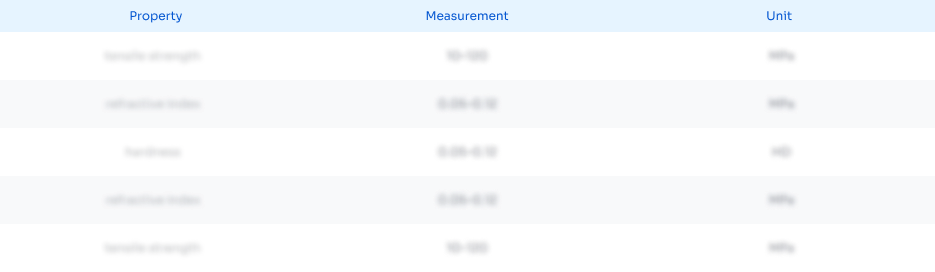
Abstract
Description
Claims
Application Information

- R&D
- Intellectual Property
- Life Sciences
- Materials
- Tech Scout
- Unparalleled Data Quality
- Higher Quality Content
- 60% Fewer Hallucinations
Browse by: Latest US Patents, China's latest patents, Technical Efficacy Thesaurus, Application Domain, Technology Topic, Popular Technical Reports.
© 2025 PatSnap. All rights reserved.Legal|Privacy policy|Modern Slavery Act Transparency Statement|Sitemap|About US| Contact US: help@patsnap.com