Method for controlling center porosity of large section heavy rail steel casting blank
A technology of center loose, heavy rail steel, applied in the field of iron and steel metallurgy, can solve the problems of shrinkage porosity and segregation, and achieve the effects of center porosity control, shrinkage elimination, and improvement of nucleation rate
- Summary
- Abstract
- Description
- Claims
- Application Information
AI Technical Summary
Problems solved by technology
Method used
Examples
Embodiment 1
[0031] In this embodiment, a steelmaking plant adopts the technical method of the present invention to produce large-section (320mm×410mm) heavy rail steel U75V continuous casting slabs. The actual control of the production process is as follows: after the vacuum treatment, the exit temperature is 56°C-65°C higher than the liquidus temperature, and the exit temperature of the first heat of the tundish is 74°C. The actual superheat control range of the tundish is 24°C to 33°C, with an average of 30°C. During the pouring process, the normal casting speed is controlled at 0.68m / min~0.72m / min, and the ratio of 0.71m / min (constant speed pouring) is up to 81.1%. The actual depression at the end of solidification is 17.2mm. The stirring intensity of the electromagnetic stirring of the crystallizer is set to 300A, and the stirring frequency is 2.4Hz; the stirring intensity of the electromagnetic stirring at the end of solidification is set to 350A, and the stirring frequency is 7.0Hz...
Embodiment 2
[0034] This embodiment is that a steelmaking plant adopts the technical method of the present invention to produce large-section (320mm×410mm) heavy rail steel U71Mn continuous casting slabs. The actual control of the production process is as follows: after the vacuum treatment, the exit temperature is 57°C to 67°C higher than the liquidus temperature, and the exit temperature of the first batch of tundish is 73°C. The actual superheat control range of the tundish is 26°C to 35°C, with an average of 31°C. During the pouring process, the normal casting speed is controlled at 0.68m / min~0.71m / min, and the ratio of 0.70m / min (constant speed pouring) is up to 77.7%. The actual depression at the end of solidification is 16.8mm. The stirring intensity of the electromagnetic stirring of the crystallizer is set to 400A, and the stirring frequency is 2.4Hz; the stirring intensity of the electromagnetic stirring at the end of solidification is set to 350A, and the stirring frequency is ...
Embodiment 3
[0037] This embodiment is that a steelmaking plant adopts the technical method of the present invention to produce large-section (320mm×410mm) heavy rail steel U78CrV continuous casting slabs. The actual control of the production process is as follows: after the vacuum treatment, the outbound temperature is 57°C to 66°C higher than the liquidus temperature, and the outbound temperature for the first heat of the tundish is 74°C. The actual superheat control range of the tundish is 26°C to 33°C, with an average of 31°C. During the pouring process, the normal casting speed is controlled at 0.69m / min~0.71m / min, and the ratio of 0.70m / min (constant speed pouring) is up to 81.8%. The actual depression at the end of solidification is 17.5mm. The stirring intensity of the electromagnetic stirring of the crystallizer is set to 350A, and the stirring frequency is 2.4Hz; the stirring intensity of the electromagnetic stirring at the solidification end is set to 350A, and the stirring fre...
PUM
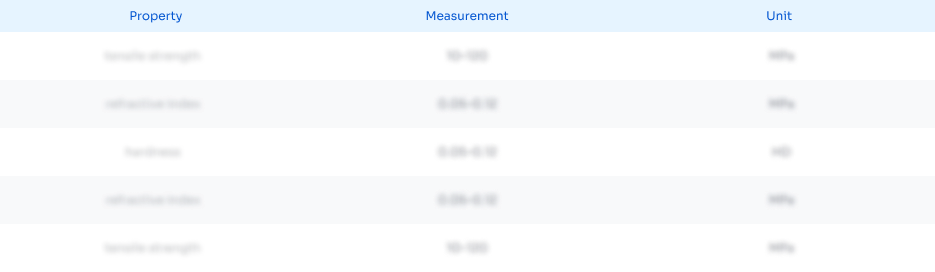
Abstract
Description
Claims
Application Information

- R&D
- Intellectual Property
- Life Sciences
- Materials
- Tech Scout
- Unparalleled Data Quality
- Higher Quality Content
- 60% Fewer Hallucinations
Browse by: Latest US Patents, China's latest patents, Technical Efficacy Thesaurus, Application Domain, Technology Topic, Popular Technical Reports.
© 2025 PatSnap. All rights reserved.Legal|Privacy policy|Modern Slavery Act Transparency Statement|Sitemap|About US| Contact US: help@patsnap.com