A kind of lignite flotation method
A technology for lignite and dry coal slime is applied in the field of coal flotation, which can solve the problems of low yield of clean coal products and poor foam stability, and achieve the effects of improving utilization efficiency, improving stability and improving flotation recovery effect.
- Summary
- Abstract
- Description
- Claims
- Application Information
AI Technical Summary
Problems solved by technology
Method used
Image
Examples
Embodiment 1
[0034] This example discloses a lignite flotation method. Lignite with an ash content of 21.53%, a moisture content of 18.75%, and a particle size of less than 0.5 mm is selected as the raw material for flotation, and coking coal with an ash content of 8.81%, ash content of 2.98%, and a particle size of less than 0.074 mm is selected. (a type of bituminous coal) as buoyant particles. A standard laboratory hanging cell unit flotation machine (1.5 L) was used to carry out the flotation test. The stirring speed of the flotation machine was 1800 rpm, and the air volume was 0.25 m 3 / h. Kerosene is used as a collector with an amount of 2 kg / t; sec-octanol is used as a foaming agent with an amount of 0.5 kg / t. The water in the test process is deionized water, and the solid mass percentage concentration of the slurry is 6%. The mass ratio of buoyant particles to lignite particles is 1:2, that is, 30g of buoyant particles and 60g of lignite particles. Specifically include the follo...
Embodiment 2
[0040]This example discloses a lignite flotation method. Lignite with an ash content of 21.53%, a moisture content of 18.75%, and a particle size of less than 0.5 mm is selected as the raw material for flotation, and coking coal with an ash content of 8.81%, ash content of 2.98%, and a particle size of less than 0.074 mm is selected. (a type of bituminous coal) as buoyant particles. A standard laboratory hanging cell unit flotation machine (1.5 L) was used to carry out the flotation test. The stirring speed of the flotation machine was 1800 rpm, and the air volume was 0.25 m 3 / h. Kerosene is used as a collector with an amount of 2 kg / t; sec-octanol is used as a foaming agent with an amount of 0.5 kg / t. The water in the test process is deionized water, and the solid mass percentage concentration of the slurry is 6%. The mass ratio of buoyant particles to lignite particles is 1:1, that is, 45g of buoyant particles and 45g of lignite particles. The specific test steps of Exam...
Embodiment 3
[0043] This example discloses a lignite flotation method. Lignite with an ash content of 21.53%, a moisture content of 18.75%, and a particle size of less than 0.5 mm is selected as the raw material for flotation, and coking coal with an ash content of 8.81%, ash content of 2.98%, and a particle size of less than 0.074 mm is selected. (a type of bituminous coal) as buoyant particles. A standard laboratory hanging cell unit flotation machine (1.5 L) was used to carry out the flotation test. The stirring speed of the flotation machine was 1800 rpm, and the air volume was 0.25 m 3 / h. Kerosene is used as a collector with an amount of 2 kg / t; sec-octanol is used as a foaming agent with an amount of 0.5 kg / t. The water in the test process is deionized water, and the solid mass percentage concentration of the slurry is 6%. The mass ratio of buoyant particles to lignite particles is 2:1, that is, 60g of buoyant particles and 30g of lignite particles. The specific test steps of Exa...
PUM
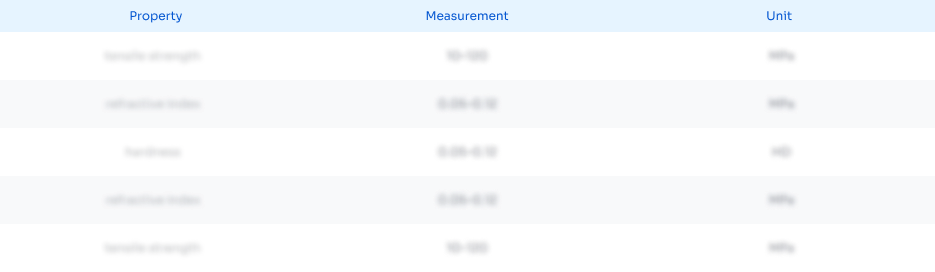
Abstract
Description
Claims
Application Information

- R&D
- Intellectual Property
- Life Sciences
- Materials
- Tech Scout
- Unparalleled Data Quality
- Higher Quality Content
- 60% Fewer Hallucinations
Browse by: Latest US Patents, China's latest patents, Technical Efficacy Thesaurus, Application Domain, Technology Topic, Popular Technical Reports.
© 2025 PatSnap. All rights reserved.Legal|Privacy policy|Modern Slavery Act Transparency Statement|Sitemap|About US| Contact US: help@patsnap.com