COREX method for reducing coal gas components through coal gas blending adjustment
A gas composition and coal blending technology, which is applied in the field of coal pyrolysis gas production and smelting reduction ironmaking process preparation, can solve the problems of low metallization rate and large coke consumption, so as to reduce coke consumption and increase reduction metallization rate , the effect of reducing production costs
- Summary
- Abstract
- Description
- Claims
- Application Information
AI Technical Summary
Problems solved by technology
Method used
Image
Examples
Embodiment 1
[0045] Three kinds of lump coal A, B, C with particle size between 5-50mm, assuming that the weight part of blending lump coal is 100, the weight part of lump coal A (Ad=5, Vd=42) is 38, and lump coal B The parts by weight of (Ad=5, Vd=26) are 18, and the parts by weight of lump coal C (Ad=3, Vd=24) are 44, and the lump coal that will be mixed in proportion is added to the melting furnace top temperature of 1050°C. In the gasification furnace, the reduced gas (1000°C) produced after pyrolysis is mixed with cold gas, adjusted to 800°C, and then enters the hot cyclone dust collector. The ore, coke, and flux added to the top of the furnace undergo a reverse reduction reaction. The reduction pressure of the gasifier is between 0.3MPa and the pure oxygen flow through the gasifier is 550NM3 / tHM. The reduced gas components and ore metals entering the shaft furnace The conversion rate and coke ratio and other indicators are shown in Table 1.
Embodiment 2
[0047] Three kinds of lump coal A, B, C with granularity between 5-55mm, assuming that the weight part of matching lump coal is 100, the weight part of lump coal A (Ad=4, Vd=39) is 40, and lump coal B (Ad=6, Vd=28) is 20 parts by weight, and the weight part of lump coal C (Ad=2, Vd=25) is 40. It is 1050 ℃ of molten In the gasification furnace, the reduced gas (1050°C) produced after pyrolysis is mixed with cold gas, adjusted to 830°C, and then enters the hot cyclone dust collector. After dust removal, the reduced gas enters the reduction shaft furnace and flows from the reduction shaft The ore, coke, and flux added to the top of the furnace undergo a reverse reduction reaction. The reduction pressure of the gasifier is between 0.33MPa and the pure oxygen flow through the gasifier is 535NM3 / tHM. The reduced gas components and ore metals entering the shaft furnace The conversion rate and coke ratio and other indicators are shown in Table 1.
Embodiment 3
[0049]Three kinds of lump coal A, B, C with granularity between 5-60mm, assuming that the weight part of blending lump coal is 100, the weight part of lump coal A (Ad=4, Vd=37) is 42, and lump coal B (Ad=5, Vd=30) is 21 parts by weight, and the weight part of lump coal C (Ad=2, Vd=26) is 37. It is 1050 DEG C melting furnace top temperature is 1050 DEG C to add the lump coal that is mixed in proportion. In the gasification furnace, the reduced gas (1100°C) produced after pyrolysis is mixed with cold gas, adjusted to 850°C, and then enters the hot cyclone dust collector. After dust removal, the reduced gas enters the reduction shaft furnace and flows from the reduction shaft The ore, coke, and flux added to the top of the furnace undergo a reverse reduction reaction. The reduction pressure of the gasifier is between 0.35MPa and the pure oxygen flow through the gasifier is 520NM3 / tHM. The reduced gas components, ore metals entering the shaft furnace The conversion rate and coke r...
PUM
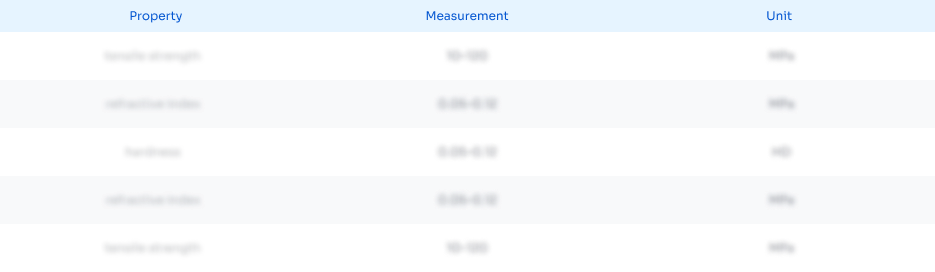
Abstract
Description
Claims
Application Information

- R&D
- Intellectual Property
- Life Sciences
- Materials
- Tech Scout
- Unparalleled Data Quality
- Higher Quality Content
- 60% Fewer Hallucinations
Browse by: Latest US Patents, China's latest patents, Technical Efficacy Thesaurus, Application Domain, Technology Topic, Popular Technical Reports.
© 2025 PatSnap. All rights reserved.Legal|Privacy policy|Modern Slavery Act Transparency Statement|Sitemap|About US| Contact US: help@patsnap.com