High-temperature curing chamber and curing technology for battery pole plates
A high-temperature curing, battery plate technology, applied in electrode manufacturing, electrode heat treatment, etc., can solve the problems of uneven curing and drying of plates, uneven circulating air in the curing room, affecting battery consistency, etc., to improve equipment utilization, Long service life, small difference effect
- Summary
- Abstract
- Description
- Claims
- Application Information
AI Technical Summary
Problems solved by technology
Method used
Image
Examples
Embodiment 1
[0024] The present invention also provides a process for high-temperature curing of battery plates through the above-mentioned high-temperature curing chamber, which includes the following steps:
[0025] In each stage of high-temperature curing and drying, the intake air door switch, humidity exhaust air door switch, humidity exhaust fan speed, atomization humidification nozzle switch, steam humidification nozzle switch, circulation fan speed, temperature and humidity monitoring, temperature and humidity and the time of each stage are controlled by PLC. . The atomization humidification and steam humidification switches are controlled according to the difference between the setting process and the actual monitoring value. When the humidity is low, the atomization humidification is turned on, when the humidity is high, the humidification is turned off, and the dehumidification is turned on. Open the automatic lifting door 19, place the coated electrode plate 15 on the curing ra...
Embodiment 2
[0033]A process for high-temperature curing of battery plates through the above-mentioned high-temperature curing chamber, comprising the following steps: in each stage of high-temperature curing and drying controlled by PLC, the switch of the air inlet door, the switch of the humidity exhaust damper, the speed of the humidity exhaust fan, the switch of the atomization humidification nozzle, Steam humidification nozzle switch, circulation fan speed, temperature and humidity monitoring, temperature and humidity and the time of each stage. The atomization humidification and steam humidification switches are controlled according to the difference between the setting process and the actual monitoring value. When the humidity is low, the atomization humidification is turned on, when the humidity is high, the humidification is turned off, and the dehumidification is turned on. Open the automatic lifting door 19, place the coated electrode plate 15 on the curing rack 14, enter the cur...
Embodiment 3
[0039] A process for high-temperature curing of battery plates through the above-mentioned high-temperature curing chamber, comprising the following steps: in each stage of high-temperature curing and drying controlled by PLC, the switch of the air inlet door, the switch of the humidity exhaust damper, the speed of the humidity exhaust fan, the switch of the atomization humidification nozzle, Steam humidification nozzle switch, circulation fan speed, temperature and humidity monitoring, temperature and humidity and the time of each stage. The atomization humidification and steam humidification switches are controlled according to the difference between the setting process and the actual monitoring value. When the humidity is low, the atomization humidification is turned on, when the humidity is high, the humidification is turned off, and the dehumidification is turned on. Open the automatic lifting door 19, place the coated electrode plate 15 on the curing rack 14, enter the cu...
PUM
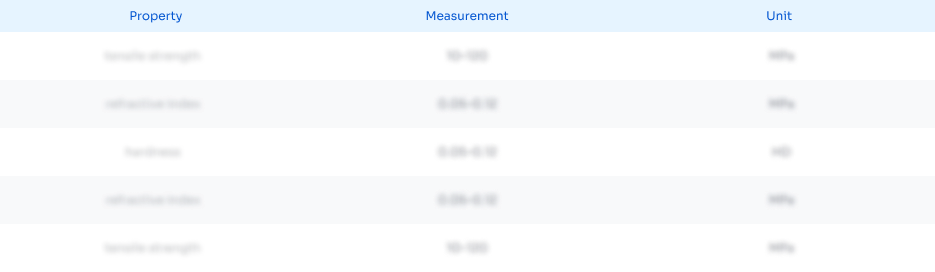
Abstract
Description
Claims
Application Information

- R&D Engineer
- R&D Manager
- IP Professional
- Industry Leading Data Capabilities
- Powerful AI technology
- Patent DNA Extraction
Browse by: Latest US Patents, China's latest patents, Technical Efficacy Thesaurus, Application Domain, Technology Topic, Popular Technical Reports.
© 2024 PatSnap. All rights reserved.Legal|Privacy policy|Modern Slavery Act Transparency Statement|Sitemap|About US| Contact US: help@patsnap.com