Acid and alkali corrosion resistant aluminum alloy section bars
An aluminum alloy profile, acid and alkali resistant technology, applied in the field of metal materials, can solve problems such as suboptimal performance, achieve the effect of eliminating harmful effects, refining recrystallized grains, and improving shaping
- Summary
- Abstract
- Description
- Claims
- Application Information
AI Technical Summary
Problems solved by technology
Method used
Image
Examples
Embodiment 1
[0020] S1: Weighing each raw material for smelting to obtain an ingot;
[0021] S2: Homogenization: Place the ingot obtained in S1 in a holding furnace at 540°C, and keep it at 540°C for 9 hours. After the holding is completed, the holding furnace is cooled to 300°C, and then air-cooled to room temperature;
[0022] S3: Remove the outer skin of the ingot car obtained in S2, and extrude it on a hydraulic press. Before extrusion, heat the extrusion cylinder, extrusion die and ingot. The profile is stretched and straightened, and the stretched and straightened profile is heat treated;
[0023] S4: Surface treatment: The heat-treated profiles completed in S3 are surface-treated according to the treatment route of surface grinding → degreasing → alkali washing → water rinsing → light emission → water rinsing → anodizing → sealing → drying, wherein the anodizing solution consists of It is 200g / L sulfuric acid + 20g / L oxalic acid + 15g / L glycerol, the anodizing temperature is 25°C, ...
Embodiment 2
[0025] S1: Weighing each raw material for smelting to obtain an ingot;
[0026] S2: Homogenization: Place the ingot obtained in S1 in a holding furnace at 580°C, and keep it at 580°C for 7 hours. After the heat preservation is completed, the holding furnace is cooled to 305°C, and then air-cooled to room temperature;
[0027] S3: Remove the outer skin of the ingot car obtained in S2, and extrude it on a hydraulic press. Before extrusion, heat the extrusion cylinder, extrusion die and ingot. The profile is stretched and straightened, and the stretched and straightened profile is heat treated;
[0028] S4: Surface treatment: The heat-treated profiles completed in S3 are surface-treated according to the treatment route of surface grinding → degreasing → alkali washing → water rinsing → light emission → water rinsing → anodizing → sealing → drying, wherein the anodizing solution consists of It is 195g / L sulfuric acid + 18g / L oxalic acid + 13g / L glycerin, anodizing temperature is ...
Embodiment 3
[0030] S1: Weighing each raw material for smelting to obtain an ingot;
[0031] S2: Homogenization: Place the ingot obtained in S1 in a holding furnace at 560°C, and keep it at 560°C for 8 hours. After the holding is completed, the holding furnace is cooled to 295°C, and then air-cooled to room temperature;
[0032] S3: Remove the outer skin of the ingot car obtained in S2, and extrude it on a hydraulic press. Before extrusion, heat the extrusion cylinder, extrusion die and ingot. The profile is stretched and straightened, and the stretched and straightened profile is heat treated;
[0033] S4: Surface treatment: The heat-treated profiles completed in S3 are surface-treated according to the treatment route of surface grinding → degreasing → alkali washing → water rinsing → light emission → water rinsing → anodizing → sealing → drying, wherein the anodizing solution consists of 205g / L sulfuric acid + 22g / L oxalic acid + 17g / L glycerin, anodizing temperature is 30°C, anodizing ...
PUM
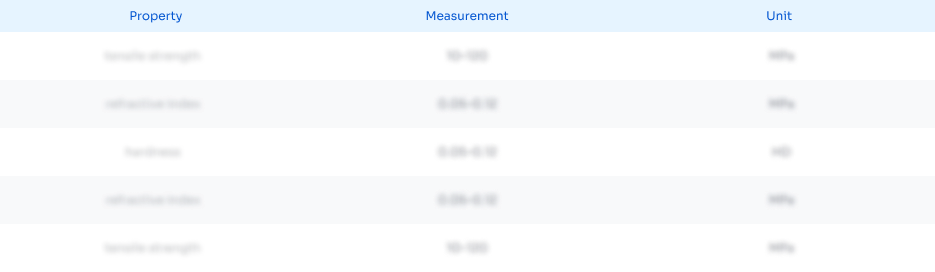
Abstract
Description
Claims
Application Information

- R&D
- Intellectual Property
- Life Sciences
- Materials
- Tech Scout
- Unparalleled Data Quality
- Higher Quality Content
- 60% Fewer Hallucinations
Browse by: Latest US Patents, China's latest patents, Technical Efficacy Thesaurus, Application Domain, Technology Topic, Popular Technical Reports.
© 2025 PatSnap. All rights reserved.Legal|Privacy policy|Modern Slavery Act Transparency Statement|Sitemap|About US| Contact US: help@patsnap.com