Heavy oil processing coking prevention method and fractionating tower
A fractionation tower, anti-coking technology, applied in the petroleum industry, hydrocarbon distillation, etc., can solve the problems of long residence time, overheating of circulating oil slurry, affecting production, etc., and achieve the effect of shortening residence time and avoiding local overheating
- Summary
- Abstract
- Description
- Claims
- Application Information
AI Technical Summary
Problems solved by technology
Method used
Image
Examples
Embodiment Construction
[0015] See figure 1 , is that the washing and desuperheating section 1 of the fractionating tower adopts the cone ring baffle plan, and the liquid guiding skirt 6 is arranged under the washing and superheating section 1 of the fractionating tower. There is a gap between the outer edge of the plate 6 and the wall of the fractionation tower 1, and the rapid cooling medium distribution pipe 4 is arranged above the liquid collecting skirt 6. An oil and gas guide pipe 8 is arranged under the washing and desuperheating section 1 of the fractionating tower, the lower end of which is connected to the oil and gas inlet 9, and the upper end is connected to the lower mouth of the bell mouth 7, and the upper mouth of the bell mouth 7 passes through the central air hole 5 and extends to the liquid collecting skirt plate 6 above.
[0016] See figure 2 , is that the washing and desuperheating section 1 of the fractionating tower adopts the herringbone baffle scheme, and the liquid guiding...
PUM
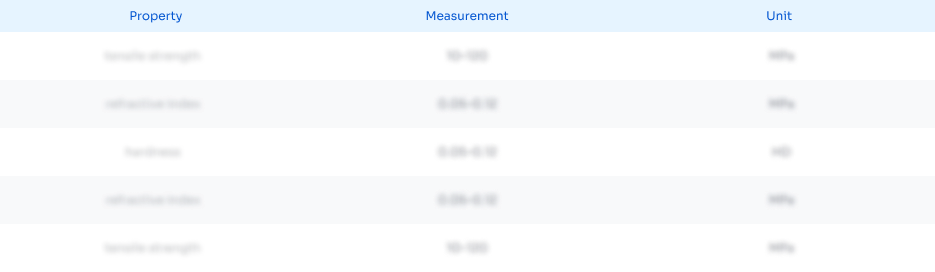
Abstract
Description
Claims
Application Information

- Generate Ideas
- Intellectual Property
- Life Sciences
- Materials
- Tech Scout
- Unparalleled Data Quality
- Higher Quality Content
- 60% Fewer Hallucinations
Browse by: Latest US Patents, China's latest patents, Technical Efficacy Thesaurus, Application Domain, Technology Topic, Popular Technical Reports.
© 2025 PatSnap. All rights reserved.Legal|Privacy policy|Modern Slavery Act Transparency Statement|Sitemap|About US| Contact US: help@patsnap.com