Process method for making building material from straw fiber and pulp
A technology of straw fiber and process method, which is applied in the field of straw fiber pulp to make building materials, can solve problems such as pollution, and achieve the effects of high strength, green environmental protection and low cost
- Summary
- Abstract
- Description
- Claims
- Application Information
AI Technical Summary
Problems solved by technology
Method used
Examples
example 1
[0020] A process for making building materials from straw fiber pulp. The building material formula includes straw fibers, talcum powder, magnesium oxide and a modifier, wherein the mass proportions of each component are straw fiber 70%; talc powder 10%; magnesium oxide 10% % and modifier 10%, the modifier is made up of sodium dodecylbenzenesulfonate, powdered activated carbon, pulping black liquor, sodium silicate and liquid paraffin, wherein the mass proportion of each component is dodecane Sodium phenyl sulfonate 10%; powdery activated carbon 30%; pulping black liquor 40%; sodium silicate 10% and liquid paraffin 10%, the Baume degree of pulping black liquor is 28°, the specific process steps are as follows:
[0021] (1) Modifier preparation: first put the pulping black liquor into a stirring container, then add sodium dodecylbenzenesulfonate, stir for ten minutes, then add sodium silicate and powdered activated carbon, and stir for fifteen minutes ,spare;
[0022] (2) Put ...
example 2
[0025] A process for making building materials from straw fiber pulp. The building material formula includes pulp, talcum powder, magnesium oxide and a modifier, wherein the mass proportions of each component are 70% of pulp; 10% of talc powder; 10% of magnesium oxide and Modifier 10%, the modifier is composed of sodium dodecylbenzenesulfonate, powdered activated carbon, pulping black liquor, sodium silicate and liquid paraffin, wherein the mass proportion of each component is dodecylbenzene Sodium sulfonate 10%; powdered activated carbon 30%; pulping black liquor 40%; sodium silicate 10% and liquid paraffin 10%, the Baume degree of pulping black liquor is 28°, the specific process steps are as follows:
[0026] (1) Modifier preparation: first put the pulping black liquor into a stirring container, then add sodium dodecylbenzenesulfonate, stir for ten minutes, then add sodium silicate and powdered activated carbon, and stir for fifteen minutes ,spare;
[0027] (2) Put the pla...
example 3
[0030] A process for making building materials from straw fiber pulp. The building material formula includes wheat straw fiber, talcum powder, magnesium oxide and a modifier, wherein the weight ratio of each component is 60% of wheat straw fiber; 15% of talc powder; 10% of magnesium oxide % and modifier 15%, the modifier is made up of sodium dodecylbenzenesulfonate, powdered activated carbon, pulping black liquor, sodium silicate and liquid paraffin, wherein the mass proportion of each component is dodecane Sodium phenyl sulfonate 10%; powdery activated carbon 30%; pulping black liquor 40%; sodium silicate 10% and liquid paraffin 10%, the Baume degree of pulping black liquor is 28°, the specific process steps are as follows:
[0031] (1) Modifier preparation: first put the pulping black liquor into a stirring container, then add sodium dodecylbenzenesulfonate, stir for ten minutes, then add sodium silicate and powdered activated carbon, and stir for fifteen minutes ,spare;
...
PUM
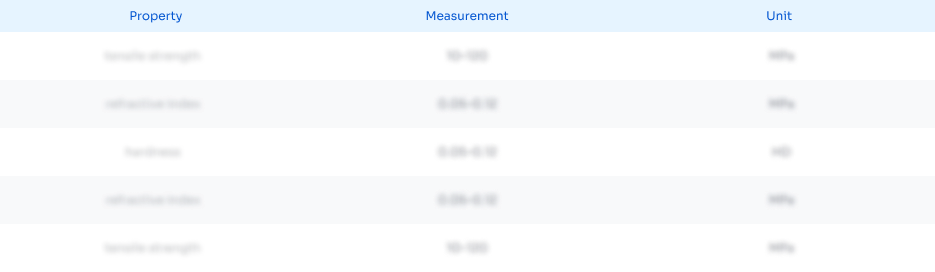
Abstract
Description
Claims
Application Information

- R&D
- Intellectual Property
- Life Sciences
- Materials
- Tech Scout
- Unparalleled Data Quality
- Higher Quality Content
- 60% Fewer Hallucinations
Browse by: Latest US Patents, China's latest patents, Technical Efficacy Thesaurus, Application Domain, Technology Topic, Popular Technical Reports.
© 2025 PatSnap. All rights reserved.Legal|Privacy policy|Modern Slavery Act Transparency Statement|Sitemap|About US| Contact US: help@patsnap.com