Method for manufacturing cabinet board
A production method and cabinet technology, which are applied in the direction of flat products, manufacturing tools, pretreatment of molding materials, etc., can solve the problems of inability to meet the diverse needs of different consumers, variability of cabinet boards, and short service life, and achieve full realization. Utilize, avoid gel effect, facilitate processing effect
- Summary
- Abstract
- Description
- Claims
- Application Information
AI Technical Summary
Problems solved by technology
Method used
Image
Examples
Embodiment l
[0029] A method for manufacturing a cabinet board, comprising the steps of:
[0030] (1) Raw material chipping: Send the residues of wood processing including slats and waste veneers to the conveyor chain, and then enter the drum chipper to chip into chips to obtain wood chips;
[0031] (2) Impurity removal and screening: Use a magnet device to remove metal objects mixed in the wood chips, screen the wood chips through a screening machine, remove debris, and separate the oversized wood chips to obtain uniform wood chips, and wash the wood chips with water washing equipment. Remove mud, sand and other impurities contained in wood chips;
[0032] (3) Cooking: Cook the wood chips obtained in step (2), so that the wood chips are cooked and softened under saturated steam with a temperature of 145° C., and the cooking time is 5 minutes;
[0033] (4) wax application heat grinding: liquid wax is applied on the wood chip after cooking, and the amount of wax applied is 0.3% of the weig...
Embodiment 2
[0042] A method for manufacturing a cabinet board, comprising the steps of:
[0043] (1) Raw material chipping: Send the residues of wood processing including slats and waste veneers to the conveyor chain, and then enter the drum chipper to chip into chips to obtain wood chips;
[0044] (2) Impurity removal and screening: Use a magnet device to remove metal objects mixed in the wood chips, screen the wood chips through a screening machine, remove debris, and separate the oversized wood chips to obtain uniform wood chips, and wash the wood chips with water washing equipment. Remove mud, sand and other impurities contained in wood chips;
[0045] (3) Cooking: Cook the wood chips obtained in step (2), so that the wood chips are softened by cooking under saturated steam with a temperature of 150° C., and the cooking time is 4 minutes;
[0046] (4) Wax application heat grinding: liquid wax is applied on the wood chips after cooking, and the amount of wax applied is 0.4% of the wei...
Embodiment 3
[0055] A method for manufacturing a cabinet board, comprising the steps of:
[0056] (1) Raw material chipping: Send the residues of wood processing including slats and waste veneers to the conveyor chain, and then enter the drum chipper to chip into chips to obtain wood chips;
[0057] (2) Impurity removal and screening: Use a magnet device to remove metal objects mixed in the wood chips, screen the wood chips through a screening machine, remove debris, and separate the oversized wood chips to obtain uniform wood chips, and wash the wood chips with water washing equipment. Remove mud, sand and other impurities contained in wood chips;
[0058] (3) Cooking: Cook the wood chips obtained in step (2), so that the wood chips are cooked and softened under saturated steam with a temperature of 155° C., and the cooking time is 2 minutes;
[0059] (4) wax application heat grinding: liquid wax is applied on the wood chip after cooking, and the amount of wax applied is 0.6% of the weig...
PUM
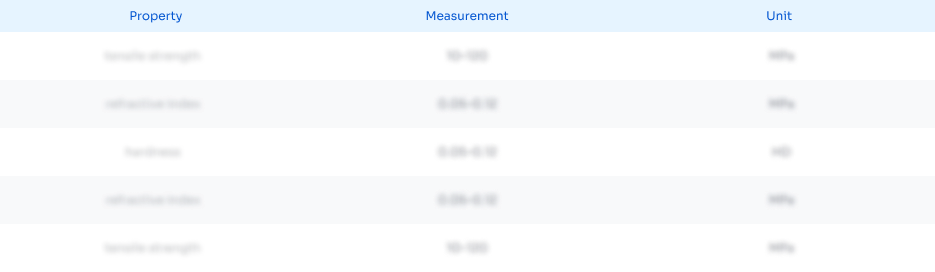
Abstract
Description
Claims
Application Information

- R&D
- Intellectual Property
- Life Sciences
- Materials
- Tech Scout
- Unparalleled Data Quality
- Higher Quality Content
- 60% Fewer Hallucinations
Browse by: Latest US Patents, China's latest patents, Technical Efficacy Thesaurus, Application Domain, Technology Topic, Popular Technical Reports.
© 2025 PatSnap. All rights reserved.Legal|Privacy policy|Modern Slavery Act Transparency Statement|Sitemap|About US| Contact US: help@patsnap.com