Cooperative control method for track online dynamic programming and weld pass tracking in welding process
A dynamic planning and welding process technology, applied in welding equipment, manufacturing tools, arc welding equipment, etc., can solve the problems of partial welding defects, difficult to take into account the dynamic response and static accuracy of mobile welding robots, and difficult to control coupling, etc.
- Summary
- Abstract
- Description
- Claims
- Application Information
AI Technical Summary
Problems solved by technology
Method used
Image
Examples
Embodiment Construction
[0038] The principle and working process of the present invention will be further described in detail below in conjunction with the accompanying drawings and embodiments.
[0039] figure 1 Shown is the flow chart of the control method for the coordination of trajectory online dynamic planning and weld bead tracking in the welding process of the present invention, including the following steps:
[0040] 1) Establish the coordinate system of the mobile welding robot system, including: the basic Cartesian coordinate system O xyz , robot body coordinate system M xyz , Airborne actuator coordinate system U xyz and the structured light sensor coordinate system L xyz , where the airborne actuator coordinate system U xyz and structured light sensor coordinate system L xyz The positive direction of the x-axis is consistent with the straight forward direction of the robot body, the positive direction of the z-axis is consistent with the direction of the ground normal, the positive ...
PUM
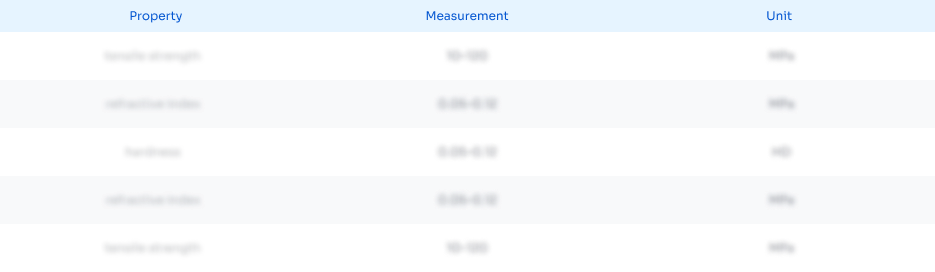
Abstract
Description
Claims
Application Information

- R&D
- Intellectual Property
- Life Sciences
- Materials
- Tech Scout
- Unparalleled Data Quality
- Higher Quality Content
- 60% Fewer Hallucinations
Browse by: Latest US Patents, China's latest patents, Technical Efficacy Thesaurus, Application Domain, Technology Topic, Popular Technical Reports.
© 2025 PatSnap. All rights reserved.Legal|Privacy policy|Modern Slavery Act Transparency Statement|Sitemap|About US| Contact US: help@patsnap.com