Rapid-densification pressure-coupling dynamic sintering furnace and sintering method
A densification and sintering furnace technology, applied in furnaces, muffle furnaces, cooking furnaces, etc., can solve the problems of difficult sliding rearrangement of particles, lack of real-time monitoring function of axial displacement, and difficulty in discharging pores, so as to prolong service life. Effect
- Summary
- Abstract
- Description
- Claims
- Application Information
AI Technical Summary
Problems solved by technology
Method used
Image
Examples
Embodiment Construction
[0025] The present invention will be described in detail below in conjunction with the accompanying drawings and embodiments.
[0026] Such as figure 1 As shown, the present invention provides a rapid densification pressure-coupled dynamic sintering furnace, which includes a furnace body 1 , a heating system 2 , a cooling system 3 , an infrared temperature measurement system 4 and a pressure coupling system 5 . The heating system 2 is located in the furnace body 1, the furnace body 1 is connected to the cooling system 3, the heating system 2 and the cooling system 3 are both connected to the infrared temperature measurement system 4, and the pressure coupling system 5 is connected to the furnace body 1.
[0027] The furnace body 1 includes a furnace shell 11, an upper furnace cover 12 and a lower furnace cover 13. The furnace shell 11 is a sandwich double-walled water-cooled structure. The inner wall of the furnace shell 11, the upper furnace cover 12 and the lower furnace cov...
PUM
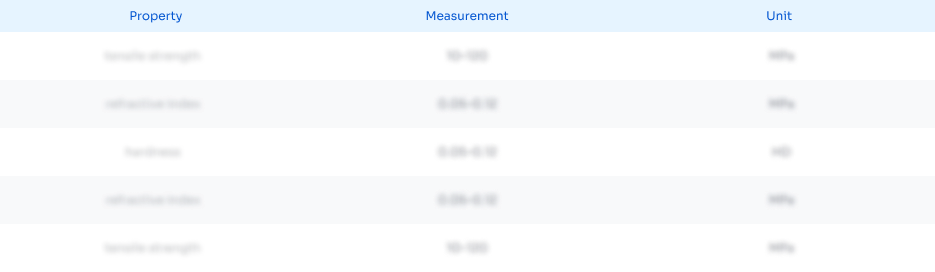
Abstract
Description
Claims
Application Information

- Generate Ideas
- Intellectual Property
- Life Sciences
- Materials
- Tech Scout
- Unparalleled Data Quality
- Higher Quality Content
- 60% Fewer Hallucinations
Browse by: Latest US Patents, China's latest patents, Technical Efficacy Thesaurus, Application Domain, Technology Topic, Popular Technical Reports.
© 2025 PatSnap. All rights reserved.Legal|Privacy policy|Modern Slavery Act Transparency Statement|Sitemap|About US| Contact US: help@patsnap.com