Low-melting-point aromatic-nitrile-group resin monomer and preparation thereof and aromatic-nitrile-group polymer and preparation method thereof
A technology of resin monomer and aromatic nitrile group, which is applied in the field of organic polymer materials, can solve the problems of high cost, narrow processing temperature window, slow thermal curing reaction, etc. Effects of Joint Points and Degree of Aggregation
- Summary
- Abstract
- Description
- Claims
- Application Information
AI Technical Summary
Problems solved by technology
Method used
Image
Examples
Embodiment
[0059] (1) A kind of synthetic method of described aromatic nitrile-based resin monomer
[0060] Step 1. Weigh the raw materials bisphenol A, DCBN and potassium carbonate on the balance. After weighing, put the three into a plastic bag and mix them evenly;
[0061] Step 2. Add 40ml of NMP into the three-necked bottle, start stirring, then add the raw materials that have been mixed in step 1, and finally add 15ml of toluene, and fill the water separator with toluene. The obtained liquid is light yellow with white particles dispersed in solution;
[0062] Step 3. Continue to heat and stir, the stirring rate is 250r / min, and the dehydration starts when the temperature is about 140°C, the color of the liquid starts to become darker, and the temperature of the solution gradually stabilizes at about 150°C under the action of toluene;
[0063] Step 4: After reacting at a constant temperature of 150°C for 2.5 hours, let go of the water and part of the toluene in the water separator t...
PUM
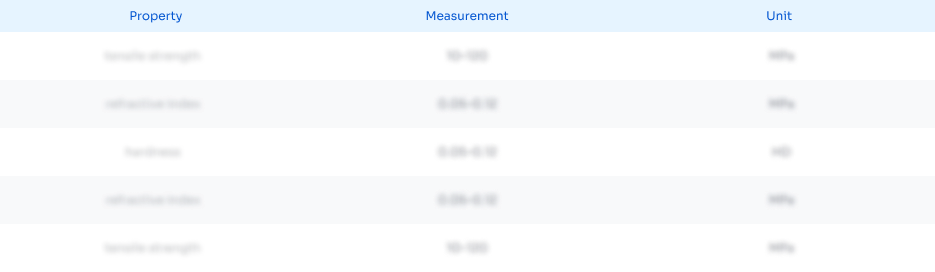
Abstract
Description
Claims
Application Information

- R&D
- Intellectual Property
- Life Sciences
- Materials
- Tech Scout
- Unparalleled Data Quality
- Higher Quality Content
- 60% Fewer Hallucinations
Browse by: Latest US Patents, China's latest patents, Technical Efficacy Thesaurus, Application Domain, Technology Topic, Popular Technical Reports.
© 2025 PatSnap. All rights reserved.Legal|Privacy policy|Modern Slavery Act Transparency Statement|Sitemap|About US| Contact US: help@patsnap.com