Ship exhaust gas denitration system
An exhaust gas and denitration technology, applied in the field of ship exhaust gas denitration system, can solve the problems of condensation, rapid aging of electric heating equipment, large power consumption, etc., and achieve the effect of improving denitration efficiency, reducing equipment corrosion, and avoiding sulfuric acid condensation.
- Summary
- Abstract
- Description
- Claims
- Application Information
AI Technical Summary
Problems solved by technology
Method used
Image
Examples
Embodiment 1
[0038] For a 72000DWT bulk carrier, the main engine power is 8000kw, the exhaust gas flow rate is 60000kg / h, and the nitrogen oxide content is 13g / kwh. Using the ship exhaust gas denitrification system of the present invention, the nitrogen oxide content of the treated exhaust gas can reach below 3g / kwh, which can meet the emission requirements of IMO for nitrogen oxides. At the same time, the power consumption saved by preheating and heat preservation of the denitrification reactor is 15kw, and no corrosion caused by sulfuric acid condensation has been found.
Embodiment 2
[0040] For a 150,000DWT crude oil tanker, the main engine power is 15,000kw, the exhaust gas flow rate is about 130,000kg / h, and the nitrogen oxide content is 13.8g / kwh. Using the ship exhaust gas denitrification system of the present invention, the nitrogen oxide content of the treated exhaust gas can reach below 3.2g / kwh, which can meet the emission requirements of IMO for nitrogen oxides. At the same time, the power consumption saved by preheating and heat preservation of the denitrification reactor is 32kw, and no corrosion caused by sulfuric acid condensation has been found.
Embodiment 3
[0042] For a 2000TEU container ship, the main engine power is 17000kw, the exhaust gas flow rate is 150000kg / h, and the nitrogen oxide concentration is 12g / kwh. Using the ship exhaust gas denitrification system of the present invention, the nitrogen oxide content of the treated exhaust gas can reach below 3g / kwh, which can meet the emission requirements of IMO for nitrogen oxides. At the same time, the power consumption saved by preheating and heat preservation of the denitrification reactor is 35kw, and no corrosion caused by sulfuric acid condensation has been found.
PUM
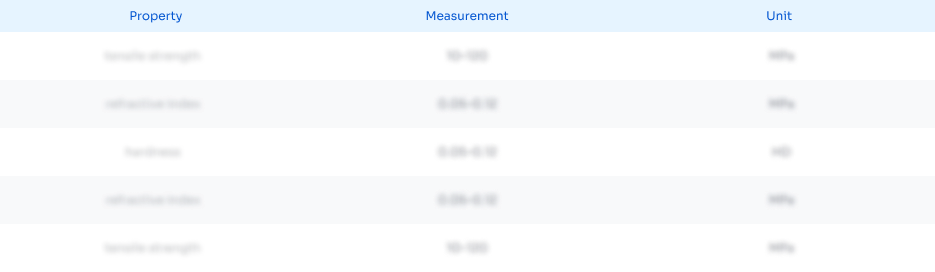
Abstract
Description
Claims
Application Information

- Generate Ideas
- Intellectual Property
- Life Sciences
- Materials
- Tech Scout
- Unparalleled Data Quality
- Higher Quality Content
- 60% Fewer Hallucinations
Browse by: Latest US Patents, China's latest patents, Technical Efficacy Thesaurus, Application Domain, Technology Topic, Popular Technical Reports.
© 2025 PatSnap. All rights reserved.Legal|Privacy policy|Modern Slavery Act Transparency Statement|Sitemap|About US| Contact US: help@patsnap.com