Treating method of tailings generated from vanadium extraction
A technology for extracting vanadium tailings and a treatment method is applied in the direction of improving process efficiency, which can solve the problems of large amount of acid solution and difficulty in wastewater treatment, and achieve the effects of reducing sodium content, being beneficial to recycling and efficient utilization.
- Summary
- Abstract
- Description
- Claims
- Application Information
AI Technical Summary
Problems solved by technology
Method used
Image
Examples
Embodiment 1
[0033] A treatment method for extracting vanadium tailings, the specific steps are as follows:
[0034] (1) adding magnesium chloride to the vanadium extraction tailings, the addition of the magnesium chloride is 3% of the vanadium extraction tailings quality, mixed uniformly;
[0035] (2) Add water to the mixture in step (1), the mass volume ratio of the mixture to water is 1g: 5mL; then place it in a reactor and react for 100min under the conditions of a temperature of 90°C and a pressure of 0.1MPa ;
[0036] (3) Separating the solid and liquid of the reaction product to obtain the immersion liquid and leaching residue. The removal rate of sodium in the leaching residue is about 47.5%.
Embodiment 2
[0038] A treatment method for extracting vanadium tailings, the specific steps are as follows:
[0039] (1) Add magnesium chloride and sodium hexametaphosphate in the tailings of vanadium extraction, the addition of described magnesium chloride is 3% of the quality of the tailings of vanadium extraction, the addition of the sodium hexametaphosphate is 2% of the quality of the tails of vanadium extraction %,well mixed;
[0040] (2) Add water to the mixture in step (1), the mass volume ratio of the mixture to water is 1g: 3mL; then place it in the reactor and react for 150min under the conditions of temperature 75°C and pressure 0.1MPa ;
[0041] (3) Separating the solid and liquid of the reaction product to obtain the immersion liquid and leaching residue. The removal rate of sodium in the leaching residue is about 62.7%.
Embodiment 3
[0043] A treatment method for extracting vanadium tailings, the specific steps are as follows:
[0044] (1) adding calcium chloride to the tailings of vanadium extraction, the addition of said calcium chloride is 8% of the quality of the tailings of vanadium extraction, mixed uniformly;
[0045] (2) Add water to the mixture in step (1), the mass volume ratio of the mixture to water is 1g: 8mL; then place it in the reactor and react for 60min under the condition that the temperature is 110°C and the pressure is 0.3MPa ;
[0046] (3) Separating the solid and liquid of the reaction product to obtain the immersion liquid and leaching residue. The removal rate of sodium in the leaching residue is about 55%.
PUM
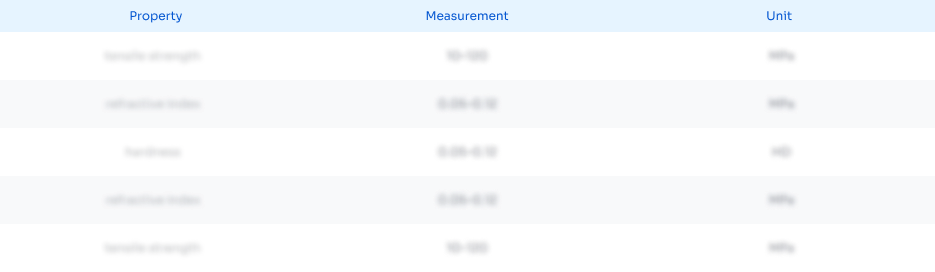
Abstract
Description
Claims
Application Information

- R&D Engineer
- R&D Manager
- IP Professional
- Industry Leading Data Capabilities
- Powerful AI technology
- Patent DNA Extraction
Browse by: Latest US Patents, China's latest patents, Technical Efficacy Thesaurus, Application Domain, Technology Topic, Popular Technical Reports.
© 2024 PatSnap. All rights reserved.Legal|Privacy policy|Modern Slavery Act Transparency Statement|Sitemap|About US| Contact US: help@patsnap.com