Preparation method of hydrotalcite-carbon black hybrid material as well as hydrotalcite-carbon black hybrid material/rubber composite material and application thereof
A hybrid material and hydrotalcite technology, applied in the field of rubber materials, can solve problems such as difficult comprehensive performance and single performance improvement, and achieve the effects of multiple cross-linking points, improved heat resistance, and improved aging performance.
- Summary
- Abstract
- Description
- Claims
- Application Information
AI Technical Summary
Problems solved by technology
Method used
Image
Examples
Embodiment 1
[0032] (1) Anhydration of hydrotalcite: Take 1g of zinc-aluminum hydrotalcite and ultrasonically disperse it in 150mL of acetone, add 1g of maleic anhydrided polybutadiene and 0.1g of p-toluenesulfonic acid, reflux at 80°C for 12h, A pale yellow anhydrided hydrotalcite was obtained.
[0033] (2) Amination of carbon black: ultrasonically disperse 1g of carbon black N330 in 150mL of acetone, add 1g of γ-aminopropyltriethoxysilane, and reflux at 80°C for 12h under nitrogen atmosphere to obtain black amino carbon black.
[0034] (3) Preparation of hydrotalcite-carbon black hybrid material: the anhydrided hydrotalcite obtained in step (1) and the aminated carbon black obtained in step (2) were ultrasonically dispersed at a ratio of 1:1 by mass to form a suspension , and uniformly mixed, coprecipitated, washed and dried to obtain a hydrotalcite-carbon black hybrid material.
[0035] (4) Preparation of hydrotalcite-carbon black / rubber composite material: take 100 mass parts of n...
Embodiment 2
[0038] (1) Anhydration of hydrotalcite: Take 1g of zinc-aluminum hydrotalcite and ultrasonically disperse it in 150mL of acetone, add 2g of maleic anhydrided polybutadiene and 0.1g of benzenesulfonic acid, and reflux at 90°C for 11h to obtain light yellow Anhydrided hydrotalcite.
[0039] (2) Amination of carbon black: Take 1g of carbon black N330 and ultrasonically disperse it in 150mL of acetone, add 3g of N-β-(aminoethyl)-γ-aminopropyltrimethoxysilane, under nitrogen atmosphere, at 90 Reflux at ℃ for 11h to obtain black aminated carbon black.
[0040] (3) Preparation of hydrotalcite-carbon black hybrid material: the anhydrided hydrotalcite obtained in step (1) and the aminated carbon black obtained in step (2) were ultrasonically dispersed in 1:5 parts by mass to form a suspension , and uniformly mixed, coprecipitated, washed and dried to obtain a hydrotalcite-carbon black hybrid material.
[0041]All the other implementations are as in Example 1.
[0042] The morpholo...
Embodiment 3
[0044] (1) Anhydride of hydrotalcite: take 1g of zinc-aluminum hydrotalcite and ultrasonically disperse it in 150mL of acetone, add 3g of maleic anhydride polybutadiene and 0.1g of 2,4-dimethylbenzenesulfonic acid, at 85℃ Under reflux for 13h, light yellow acid anhydride hydrotalcite was obtained.
[0045] (2) Amination of carbon black: ultrasonically disperse 1g of carbon black N330 in 150mL of acetone, add 6g of g-aminopropyltrimethoxysilane, and reflux at 80°C for 12h under a nitrogen atmosphere to obtain black amination carbon black.
[0046] (3) Preparation of hydrotalcite-carbon black hybrid material: the anhydrided hydrotalcite obtained in step (1) and the aminated carbon black obtained in step (2) were ultrasonically dispersed at a ratio of 1:15 to form a suspension , and uniformly mixed, coprecipitated, washed and dried to obtain a hydrotalcite-carbon black hybrid material.
[0047] All the other implementations are as in Example 1.
[0048] The morphology and st...
PUM
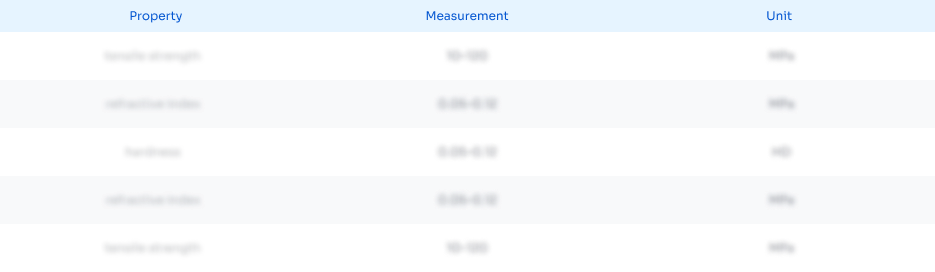
Abstract
Description
Claims
Application Information

- R&D
- Intellectual Property
- Life Sciences
- Materials
- Tech Scout
- Unparalleled Data Quality
- Higher Quality Content
- 60% Fewer Hallucinations
Browse by: Latest US Patents, China's latest patents, Technical Efficacy Thesaurus, Application Domain, Technology Topic, Popular Technical Reports.
© 2025 PatSnap. All rights reserved.Legal|Privacy policy|Modern Slavery Act Transparency Statement|Sitemap|About US| Contact US: help@patsnap.com