Method for preventing nitrogen increment of LF refined low-nitrogen steel
A low-nitrogen steel and converter technology, applied in the field of low-nitrogen steel smelting, can solve the problems of high argon cost, high cost, and difficult implementation, and achieve the effects of low production cost, reduced nitrogen increase, and reduced nitrogen increase amount
- Summary
- Abstract
- Description
- Claims
- Application Information
AI Technical Summary
Problems solved by technology
Method used
Examples
Embodiment 1
[0022] Embodiment 1: The method for refining low-nitrogen steel in this LF furnace to prevent nitrogen increase adopts the following specific processes.
[0023] 125 tons of molten steel tapped from the converter enters the station without encrustation, the entry temperature is 1493 degrees, the steel type is XY77B, and the N content before refining is 13ppm; according to the key requirements before the furnace, 400kg of fine ash and 200kg of fluorite are added during the tapping process. Large argon stirring is not allowed when entering the refining station, and the argon gas is controlled at 50Nm / l. Flow rate) is controlled at 86Nm / l, the supplementary component is controlled at argon flow rate of 157Nm / l, and the dissolution of carbon powder is promoted by means of electrode heating. The flow of argon gas is controlled at 36Nm / l by soft blowing. The process heating adopts 4 gears and 36000 heating mode. After the treatment is completed, the silicon-calcium line is fed for 3...
Embodiment 2
[0024] Embodiment 2: The method for refining low-nitrogen steel in this LF furnace to prevent nitrogen increase adopts the following specific process.
[0025] Adopt 125 tons LF refining furnace. The molten steel tapped from the converter enters the station without encrustation, the entry temperature is 1482 degrees, the steel type is XY77B, and the N content before refining is 20ppm; 450kg of small grain ash and 200kg of fluorite are added during the tapping process according to the key requirements before the furnace. Large argon stirring is not allowed in the refining station, and the argon gas is controlled at 40Nm / l. The order of feeding into the station is: 160kg of fluorite, 225kg of submerged arc slag, 425kg of small ash, 62.5kg of calcium carbide, and 87.5kg of deoxidizer; (Actual flow rate) is controlled at 90Nm / l, and the argon gas flow rate is controlled at 146Nm / l by supplementary components, and the dissolution of carbon powder is promoted by means of electrode h...
Embodiment 3
[0026] Embodiment 3: The method for refining low-nitrogen steel in this LF furnace to prevent nitrogen increase adopts the following specific process.
[0027] Adopt 125 tons LF refining furnace. The molten steel tapped from the converter enters the station without crust, the entry temperature is 1490 degrees, the steel type is XY77B, and the N content before refining is 15ppm; according to the key requirements before the furnace, 500kg of small grain ash and 200kg of fluorite are added during the tapping process. Large argon stirring is not allowed in the refining station, and the argon gas is controlled at 60Nm / l. The order of feeding into the station is: 200kg of fluorite, 210kg of submerged arc slag, 398kg of small ash, 31.25kg of calcium carbide, and 96kg of deoxidizer; during the heating process, argon ( The actual flow rate) is controlled at 88Nm / l, the argon gas flow rate is controlled at 150Nm / l, and the dissolution of carbon powder is promoted by means of electrode h...
PUM
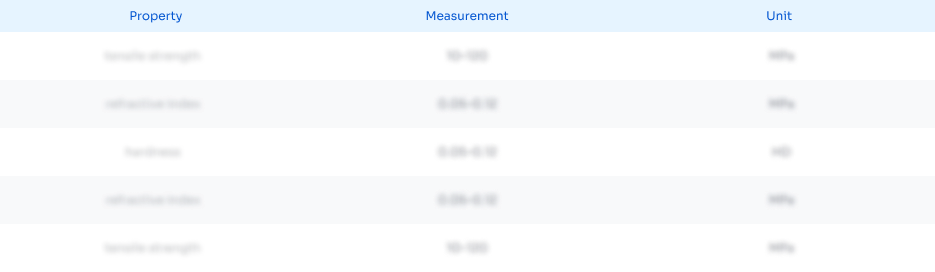
Abstract
Description
Claims
Application Information

- R&D
- Intellectual Property
- Life Sciences
- Materials
- Tech Scout
- Unparalleled Data Quality
- Higher Quality Content
- 60% Fewer Hallucinations
Browse by: Latest US Patents, China's latest patents, Technical Efficacy Thesaurus, Application Domain, Technology Topic, Popular Technical Reports.
© 2025 PatSnap. All rights reserved.Legal|Privacy policy|Modern Slavery Act Transparency Statement|Sitemap|About US| Contact US: help@patsnap.com