Composite high polymer material for kitchen top plates and preparation method thereof
A composite polymer and top plate technology, applied in the field of polymer materials and their preparation, polymer materials for kitchen top plates and their preparation, to achieve good pressure bearing effect, improve tensile strength and notched impact strength, and improve safety performance
- Summary
- Abstract
- Description
- Claims
- Application Information
AI Technical Summary
Problems solved by technology
Method used
Examples
Embodiment 1
[0041] (1) Take 20 parts of polyvinyl chloride resin, 8 parts of styrene-modified alkyd resin, 7 parts of polymethylphenyl silicone resin, 9 parts of polyperfluoroethylene propylene resin, and acetyl tributyl citrate by weight. 2.5 parts, 6 parts of hydroxypropyl cellulose, put the above materials into the mixing tank, heat and stir;
[0042] (2) Add 4 parts of tetraisopropyl titanate and 10 parts of polymethyl methacrylate to the material stirred in step (1), and then stir until uniform;
[0043] (3) Extrude the material evenly stirred in step (2) with a twin-screw extruder. The head temperature of the twin-screw extruder is 185°C. The twin-screw extrusion is divided into 4 zones, and the temperature of the first zone is 170°C. ℃, the temperature in the second zone is 185°C, the temperature in the third zone is 195°C, the temperature in the fourth zone is 220°C, the length-to-diameter ratio of the twin-screw extruder is 25:1, and pelletized after extrusion to prepare the kitc...
Embodiment 2
[0045] (1) Take 14 parts of polyvinyl chloride resin, 12 parts of styrene-modified alkyd resin, 4 parts of polymethylphenyl silicone resin, 5 parts of polyperfluoroethylene propylene resin, and acetyl tributyl citrate by weight. 4.5 parts, 3 parts of hydroxypropyl cellulose, put the above materials into the mixing tank, heat and stir;
[0046] (2) Add 2 parts of tetraisopropyl titanate and 5 parts of polymethyl methacrylate to the material stirred in step (1), and then stir until uniform;
[0047] (3) Extrude the material evenly stirred in step (2) with a twin-screw extruder. The head temperature of the twin-screw extruder is 165°C. The twin-screw extrusion is divided into 4 zones, and the temperature of the first zone is 155°C. ℃, the temperature in the second zone is 175°C, the temperature in the third zone is 205°C, the temperature in the fourth zone is 230°C, the length-to-diameter ratio of the twin-screw extruder is 15:1, and pelletized after extrusion to prepare the kitc...
Embodiment 3
[0049] (1) Take 19 parts of polyvinyl chloride resin, 9 parts of styrene-modified alkyd resin, 6 parts of polymethylphenyl silicone resin, 8 parts of polyperfluoroethylene propylene resin, and acetyl tributyl citrate by weight. 3.5 parts, 4 parts of hydroxypropyl cellulose, put the above materials into the mixing tank, heat and stir;
[0050] (2) Add 4 parts of tetraisopropyl titanate and 6 parts of polymethyl methacrylate to the material stirred in step (1), and then stir until uniform;
[0051] (3) Extrude the material evenly stirred in step (2) with a twin-screw extruder. The head temperature of the twin-screw extruder is 185°C. The twin-screw extrusion is divided into 4 zones, and the temperature of the first zone is 170°C. ℃, the temperature in the second zone is 185°C, the temperature in the third zone is 195°C, the temperature in the fourth zone is 220°C, the length-to-diameter ratio of the twin-screw extruder is 25:1, and pelletized after extrusion to prepare the kitch...
PUM
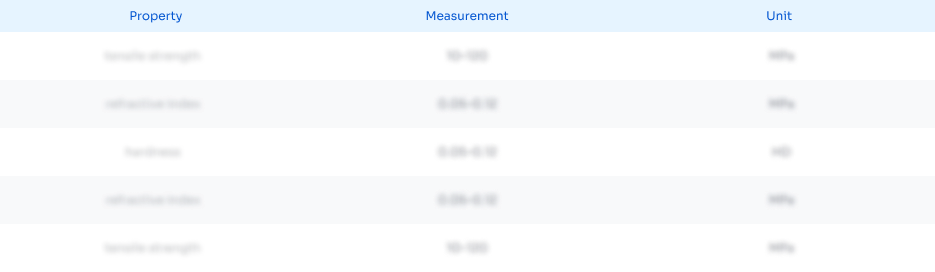
Abstract
Description
Claims
Application Information

- R&D Engineer
- R&D Manager
- IP Professional
- Industry Leading Data Capabilities
- Powerful AI technology
- Patent DNA Extraction
Browse by: Latest US Patents, China's latest patents, Technical Efficacy Thesaurus, Application Domain, Technology Topic, Popular Technical Reports.
© 2024 PatSnap. All rights reserved.Legal|Privacy policy|Modern Slavery Act Transparency Statement|Sitemap|About US| Contact US: help@patsnap.com