Porous material with central symmetry structure and method for preparing the same
A porous material and centrosymmetric technology, which is applied to home appliances, ceramic products, and other home appliances, can solve the problems of random distribution of pore structure and strength, and achieve the solution of random distribution of pore structure and low strength. The preparation method is simple and easy to operate. Good mechanical properties and stability
- Summary
- Abstract
- Description
- Claims
- Application Information
AI Technical Summary
Problems solved by technology
Method used
Image
Examples
preparation example Construction
[0031] The present invention also provides a method for preparing the above-mentioned porous material with a centrosymmetric structure, comprising the following steps:
[0032] Step 1, weigh ceramic powder, water, dispersant and binder, the volume ratio of ceramic powder and water is 1:1.5~1:4, the mass of dispersant accounts for 2%~of the total mass of ceramic powder and water 8%, the mass of the binder accounts for 1% to 4% of the total mass of the ceramic powder and water;
[0033] Step 2: Add dispersant and binder into water, mix well, then add ceramic powder, mix well to obtain raw material liquid; use zirconia balls or alumina balls as ball milling medium, ball mill in polyethylene ball mill bottle for 24 hours to make it uniform Disperse to obtain slurry;
[0034] Step 3, inject the slurry into a cylindrical mold whose sides and bottom are heat transfer materials, and then place the mold on the freezer shelf of the freeze dryer to freeze for 2-4 hours, and the freezing...
Embodiment 1
[0042] In 60g of distilled water, add 3.96g of sodium polyacrylate and 1.98g of carboxymethyl cellulose in sequence, mix evenly, and then add 138.40g of Al 2 o 3 Powder, Al 2 o 3 The volume ratio of powder and distilled water is 4:6, using zirconia balls as the ball milling medium, ball milling in a polyethylene ball mill bottle for 24 hours to make it uniformly dispersed, and the volume concentration of 40% Al 2 o 3 slurry; Al 2 o 3 The slurry is injected into a cylindrical mold with copper sides and bottom, a radius of 16mm, and a height of 48mm, and then injected with Al 2 o 3 The bottom of the slurry mold was placed on a freezing shelf at -30°C for freezing; Al 2 o 3 After the slurry was completely frozen, it was taken out, and placed in an environment with a pressure of 0Pa and dried under low pressure to obtain Al 2 o 3 Porous material preform; the Al 2 o 3 Al 2 o 3 porous material.
[0043] figure 2 is the Al prepared in Example 1 of the present inventi...
Embodiment 2
[0045] Add 5.74g sodium methylene dinaphthalene sulfonate and 2.87g polyvinyl alcohol in sequence to 70g water, mix evenly, then add 73.62g HA powder, the volume ratio of HA powder and distilled water is 3:7, use zirconia balls as the ball milling medium , ball milled in a polyethylene ball mill bottle for 24h to make it evenly dispersed, to obtain a HA slurry with a volume concentration of 30%; inject the HA slurry into a cylindrical mold with silver sides and bottom surfaces, a radius of 8mm, and a height of 24mm, and then Place the bottom of the mold injected with HA slurry on a freezing shelf at -40°C for freezing; take out the HA slurry after it is completely frozen, and place it in an environment with a pressure of 600Pa to dry it under low pressure to obtain a preformed body of HA porous material; The preform is sintered at 1250°C in an air atmosphere to obtain a HA porous material.
[0046] Each channel of the HA porous material points to the center and is evenly distr...
PUM
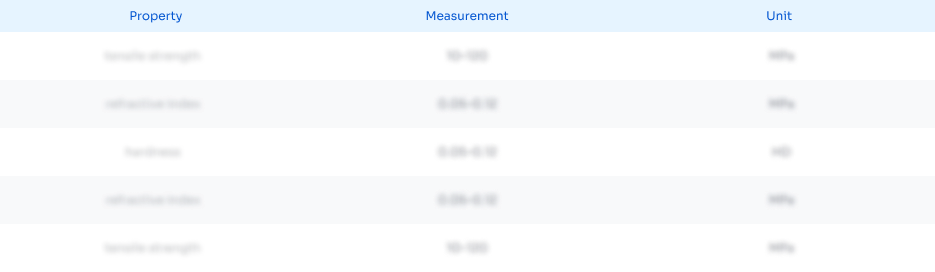
Abstract
Description
Claims
Application Information

- Generate Ideas
- Intellectual Property
- Life Sciences
- Materials
- Tech Scout
- Unparalleled Data Quality
- Higher Quality Content
- 60% Fewer Hallucinations
Browse by: Latest US Patents, China's latest patents, Technical Efficacy Thesaurus, Application Domain, Technology Topic, Popular Technical Reports.
© 2025 PatSnap. All rights reserved.Legal|Privacy policy|Modern Slavery Act Transparency Statement|Sitemap|About US| Contact US: help@patsnap.com