Diesel hydro-refining catalyst and preparation method thereof
A technology for hydrorefining and catalyst, which is applied in catalyst carriers, chemical instruments and methods, metal/metal oxide/metal hydroxide catalysts, etc., can solve the problems of increasing equipment cost, reducing product quality, and increasing side reactions, etc. Achieve the effect of low bulk density, high activity and large specific surface area
- Summary
- Abstract
- Description
- Claims
- Application Information
AI Technical Summary
Problems solved by technology
Method used
Examples
Embodiment 1
[0028] Add 110 grams of urea and 25 mg of nickel nitrate to 1500 ml of distilled water to make an aqueous solution, add 45 ml of tetraethyl orthosilicate to the above solution and stir until it becomes transparent, then add 110 ml of pseudo-both aluminum dropwise, stir evenly, and let it stand for 1- After 2 hours, a gel is formed. Heat the gel to 60-70°C, add 80 mg of ammonium molybdate, raise the temperature to 90-95°C, and react for 7-9 hours; filter, dry, and roast to obtain a diesel hydrorefining catalyst.
[0029] The activity of the catalyst was evaluated in a high-pressure hydrogenation microreactor. The reactant was diesel oil with a sulfur content of 6800ppm. 10mg of the catalyst was added. Under the conditions of 320°C, 6Mp, and a hydrogen-to-oil ratio of 500:1, the desulfurization rate was 97%.
Embodiment 2
[0031] Add 110 grams of urea and 25 mg of nickel nitrate to 1500 ml of distilled water to make an aqueous solution, add 45 ml of tetraethyl orthosilicate to the above solution and stir until it becomes transparent, then add 135 ml of pseudoboth aluminum dropwise, stir evenly, and let it stand for 1- After 2 hours, a gel is formed. Heat the gel to 60-70°C, add 70 mg of ammonium molybdate, raise the temperature to 90-95°C, and react for 7-9 hours; filter, dry, and roast to obtain a diesel hydrorefining catalyst.
[0032] The activity of the catalyst was evaluated in a high-pressure hydrogenation microreactor. The reactant was diesel oil with a sulfur content of 6800ppm, and 10mg of the catalyst was added. Under the conditions of 320°C, 6Mp, and a hydrogen-to-oil ratio of 500:1, the desulfurization rate was detected to be 95%.
Embodiment 3
[0034] Add 110 grams of urea and 25 mg of nickel nitrate to 1500 ml of distilled water to make an aqueous solution, add 45 ml of tetraethyl orthosilicate to the above solution and stir until it becomes transparent, then add 110 ml of pseudo-both aluminum dropwise, stir evenly, and let it stand for 1- After 2 hours, a gel is formed. Heat the gel to 60-70°C, add 80 mg of ammonium molybdate, raise the temperature to 90-95°C, and react for 7-9 hours; filter, dry, and roast to obtain a diesel hydrorefining catalyst.
[0035] The activity of the catalyst was evaluated in a high-pressure hydrogenation microreactor. The reactant was diesel oil with a sulfur content of 6800ppm. After adding 10mg of the catalyst, the desulfurization rate was 99.3% at 330°C, 6.2Mp, and a hydrogen-to-oil ratio of 600:1.
PUM
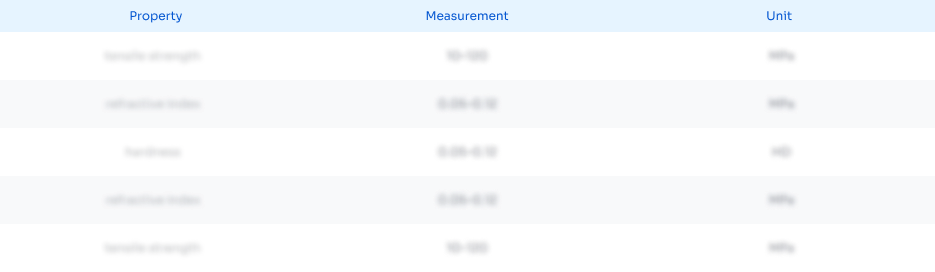
Abstract
Description
Claims
Application Information

- Generate Ideas
- Intellectual Property
- Life Sciences
- Materials
- Tech Scout
- Unparalleled Data Quality
- Higher Quality Content
- 60% Fewer Hallucinations
Browse by: Latest US Patents, China's latest patents, Technical Efficacy Thesaurus, Application Domain, Technology Topic, Popular Technical Reports.
© 2025 PatSnap. All rights reserved.Legal|Privacy policy|Modern Slavery Act Transparency Statement|Sitemap|About US| Contact US: help@patsnap.com