A kind of preparation method and application of graphene-coated metal nanoparticle catalyst
A technology coated with metal nanoparticles and graphene, applied in chemical instruments and methods, physical/chemical process catalysts, nanotechnology, etc., can solve the problems of easy agglomeration of metal nanoparticles, poor stability of Pt-based electrocatalysts, and low degree of graphitization and other problems, to achieve the effect of simple and effective operation method, conducive to large-scale production, and simple preparation process
- Summary
- Abstract
- Description
- Claims
- Application Information
AI Technical Summary
Problems solved by technology
Method used
Image
Examples
Embodiment 1
[0036] Example 1: Fe 8% -N 0.5 -CNT-E 2 -24-600 (Fe 8% Refers to the mass content of Fe in the material is 8%, N 0.5 Refers to the quality of nitrogen source melamine is 0.5 times that of carboxylated carbon nanotubes, E 2 Refers to the quality of EDTA disodium salt is twice that of iron salt, 24 refers to the hydrothermal reaction time of 24h, 600 refers to the calcination temperature of 600°C)
[0037] Add 0.1000g of carboxylated carbon nanotubes, 0.0386g of ferric chloride and 0.0500g of melamine to a mixed solution of 30mL of water and ethanol, ultrasonically disperse it for 30min, then magnetically stir at 50°C for 2h, then take 0.0772g of ethylenediamine Disodium tetraacetate and 10 mL of methanol were added to the above mixed solution and reacted hydrothermally at 150 °C for 24 hours, washed, filtered, and dried in vacuum at 80 °C to obtain the composite material Fe 8% -N 0.5 -CNT@EDTA-24;
[0038] Put the above materials in N 2 At 3°C min under atmosphere -1...
Embodiment 2
[0039] Example 2: Fe 8% -N 1 -CNT-E 2 -24-600 (Fe 8% Refers to the mass content of Fe in the material is 8%, N 1 Refers to the quality of nitrogen source melamine is 1 times that of carboxylated carbon nanotubes, E 2 Refers to the quality of EDTA disodium salt is twice that of iron salt, 24 refers to the hydrothermal reaction time of 24h, 600 refers to the calcination temperature of 600°C)
[0040] Add 0.1000g of carboxylated carbon nanotubes, 0.0386g of ferric chloride and 0.1000g of melamine to a mixed solution of 30mL of water and ethanol, disperse it evenly by ultrasonication for 30min, then magnetically stir at 50°C for 2h, and then take 0.0772g of ethylenediamine Disodium tetraacetate and 10 mL of methanol were added to the above mixed solution and reacted hydrothermally at 150 °C for 24 hours, washed, filtered, and dried in vacuum at 80 °C to obtain the composite material Fe 8% -N 1 -CNT@EDTA-24;
[0041] Put the above materials in N 2 At 3°C min under atmosph...
Embodiment 3
[0042] Example 3: Fe 8% -N 1.25 -CNT-E 2 -24-600 (Fe 8% Refers to the mass content of Fe in the material is 8%, N 1.25 Refers to the quality of nitrogen source melamine is 1.25 times that of carboxylated carbon nanotubes, E 2 Refers to the mass of EDTA disodium salt is twice that of iron salt, 24 refers to the hydrothermal reaction time of 24h, 600 refers to the calcination temperature of 600°C)
[0043] Add 0.1000g of carboxylated carbon nanotubes, 0.0386g of ferric chloride and 0.1250g of melamine to a mixed solution of 30mL of water and ethanol, ultrasonically disperse it for 30min, then magnetically stir at 50°C for 2h, then take 0.0772g of ethylenediamine Disodium tetraacetate and 10 mL of methanol were added to the above mixed solution and reacted hydrothermally at 150 °C for 24 hours, washed, filtered, and dried in vacuum at 80 °C to obtain the composite material Fe 8% -N 1.25 -CNT@EDTA-24;
[0044] Put the above materials in N 2 At 3°C min under atmosphere -...
PUM
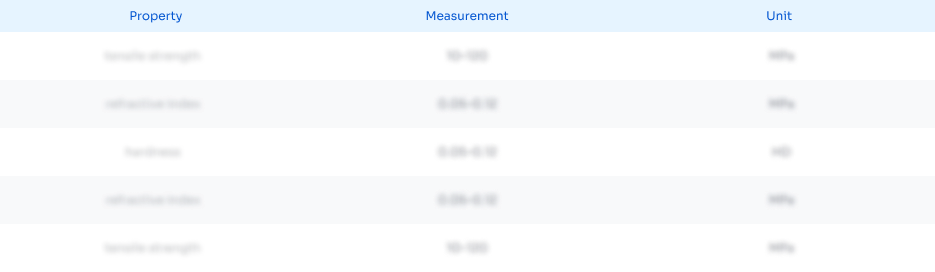
Abstract
Description
Claims
Application Information

- R&D
- Intellectual Property
- Life Sciences
- Materials
- Tech Scout
- Unparalleled Data Quality
- Higher Quality Content
- 60% Fewer Hallucinations
Browse by: Latest US Patents, China's latest patents, Technical Efficacy Thesaurus, Application Domain, Technology Topic, Popular Technical Reports.
© 2025 PatSnap. All rights reserved.Legal|Privacy policy|Modern Slavery Act Transparency Statement|Sitemap|About US| Contact US: help@patsnap.com