Low-temperature anti-corrosion gas nitriding method for metal workpiece and metal workpiece
A metal workpiece, gas nitriding technology, applied in the field of chemistry, can solve the problem of unsolved problems such as harmful application defects, and achieve the effects of shortening the nitriding cycle period, reducing the nitriding temperature, and improving the corrosion resistance.
- Summary
- Abstract
- Description
- Claims
- Application Information
AI Technical Summary
Problems solved by technology
Method used
Image
Examples
Embodiment 1
[0025] The metal workpiece in this embodiment is industrial pure iron, 300 DEG C * 9H low-temperature corrosion-resistant nitriding. The chemical composition (mass fraction, %) of the industrial pure iron is: C≤0.003, P≤0.01, S≤0.006, Si≤0.01, Mn≤0.10.
[0026] The industrial pure iron sample was processed into a block sample of 15×10×5mm by wire cutting, annealed at 1033K for 2 hours, and then the surface of the sample was ground from coarse to fine with metallographic sandpaper. Then put it into the electrolyte for electrodeposition pretreatment. The electrodeposition pretreatment uses a two-way adjustable AC power supply, with a pure iron sample as the cathode and an inert electrode as the anode. The electrodeposition pretreatment pretreatment parameters are shown in Table 1 .
[0027] Table 1 Bidirectional adjustable AC power electrodeposition pretreatment parameters
[0028]
[0029] After the pure iron sample pretreated by electrodeposition was ultrasonically cleane...
Embodiment 2
[0031] The metal workpiece in this embodiment is No. 45 steel, 400 ℃ * 6H low-temperature corrosion-resistant nitriding, and this No. 45 steel chemical composition (mass fraction, %) is: C 0.46, Si 0.25, Mn 0.68%, P≤0.04, S≤0.04, Cr≤0.25, Ni≤0.2, after quenching and tempering treatment (quenching at 1123K, tempering at 873K), process No. 45 steel into a 10×8×5mm block sample by wire cutting, annealing at 1033K for 2 hours, In this way, use 0#, 2#, 4#, 6# metallographic sandpaper to polish and smooth it. Rinse with tap water, then degrease and derust with acetone and 5% HCl, rinse and dry with distilled water and alcohol after treatment. Afterwards, the No. 45 steel sample was put into the electrolyte for electrodeposition pretreatment. The electrodeposition pretreatment used a two-way adjustable AC power supply, with the No. 45 steel sample as the cathode and the inert electrode as the anode. The electrodeposition pretreatment The processing pre-parameters are listed in Table...
Embodiment 3
[0036] The metal workpiece in this embodiment is 38CrMoAl steel, 450 ℃ * 6H low-temperature corrosion-resistant nitriding. The chemical composition (mass fraction, %) of the 38CrMoAl steel is shown in Table 3 below.
[0037] Table 3 Chemical composition of 38CrMoAl steel (mass fraction, %)
[0038] Grade
C
Si
mn
Cr
Mo
Al
38CrMoAl
0.35~0.42
0.20~0.45
0.30~0.60
1.35~1.65
0.15~0.25
0.70~1.10
[0039] After the 38CrMoAl steel sample has been quenched and tempered, the sample is processed into a 10×8×5mm block sample by wire cutting, annealed at 1033K for 2 hours, and 0#, 2#, 4#, 6# gold Smooth with sandpaper. Rinse with tap water, then degrease and rust with acetone and 10% HCl, rinse and dry with distilled water and alcohol after treatment. Then put the 38CrMoAl steel sample into the electrolyte for electrodeposition pretreatment. The electrodeposition pretreatment uses a two-way adjustable pulse power supp...
PUM
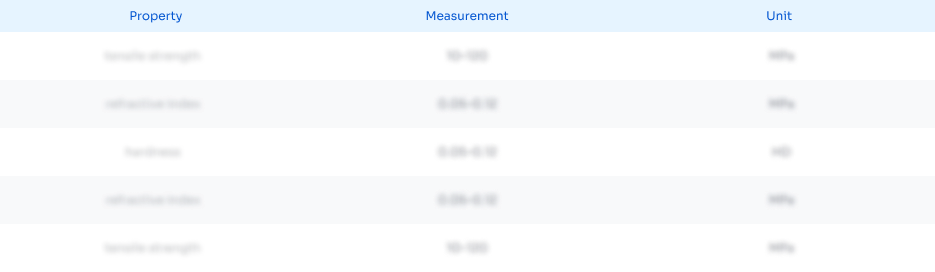
Abstract
Description
Claims
Application Information

- R&D
- Intellectual Property
- Life Sciences
- Materials
- Tech Scout
- Unparalleled Data Quality
- Higher Quality Content
- 60% Fewer Hallucinations
Browse by: Latest US Patents, China's latest patents, Technical Efficacy Thesaurus, Application Domain, Technology Topic, Popular Technical Reports.
© 2025 PatSnap. All rights reserved.Legal|Privacy policy|Modern Slavery Act Transparency Statement|Sitemap|About US| Contact US: help@patsnap.com