Anti-crack sand mold coating
A sand coating, anti-crack technology, applied in coatings, molds, cores, etc., can solve problems such as cracking of sand coatings, achieve the effects of not easy to crack, improve permeability, and reduce sand sticking defects
- Summary
- Abstract
- Description
- Claims
- Application Information
AI Technical Summary
Problems solved by technology
Method used
Image
Examples
Embodiment 1
[0032] Embodiment one: a kind of water glass graphite coating (prepared by 100kg), comprises following material: amorphous graphite powder 14kg, flaky graphite powder 6kg, water glass 5kg, water 75kg, the amorphous graphite powder that weighs and Place the flake graphite powder in a stirring container, then slowly add the weighed mixed solution of water glass and water, and stir while adding the mixed solution until the graphite powder and the mixed solution are fully mixed to form a slurry.
Embodiment 2
[0033] Embodiment two: a kind of water glass graphite coating (by 100kg preparation), comprises following material: amorphous graphite powder 20kg, flake graphite powder 5kg, water glass 9kg, water 65kg, bentonite 1kg, will weigh the amorphous Graphite powder and flaky graphite powder are placed in a stirring container, and then slowly add a weighed mixed solution of water glass, water and bentonite, and stir while adding the mixed solution until the graphite powder and the mixed solution are fully mixed to form a slurry.
Embodiment 3
[0034] Embodiment three: a kind of water glass graphite coating (by 100kg preparation), comprises following material: amorphous graphite powder 15.4kg, flake graphite powder 6.6kg, water glass 8kg, water 69kg, bentonite 0.8kg, surfactant JFC. .2kg, place the weighed amorphous graphite powder and flaky graphite powder in the stirring container, then slowly add the weighed mixed solution of water glass, water, bentonite, and surfactant JFC, and add the mixed solution while adding Stir until the graphite powder and the mixture are fully mixed to form a slurry.
PUM
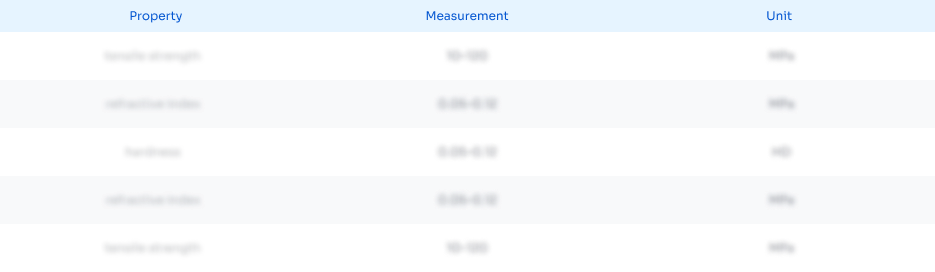
Abstract
Description
Claims
Application Information

- R&D Engineer
- R&D Manager
- IP Professional
- Industry Leading Data Capabilities
- Powerful AI technology
- Patent DNA Extraction
Browse by: Latest US Patents, China's latest patents, Technical Efficacy Thesaurus, Application Domain, Technology Topic, Popular Technical Reports.
© 2024 PatSnap. All rights reserved.Legal|Privacy policy|Modern Slavery Act Transparency Statement|Sitemap|About US| Contact US: help@patsnap.com