Dyeing and finishing process of cuproammonia viscose acetate fiber fabric
An acetate fiber and viscose technology, applied in the field of fabric dyeing, can solve the problems of poor alkali resistance, inconsistent acid and alkali resistance, and poor dimensional stability of acetate fiber, and achieve the effects of not easy to wrinkle, good drape, and high strength
- Summary
- Abstract
- Description
- Claims
- Application Information
AI Technical Summary
Problems solved by technology
Method used
Examples
Embodiment 1
[0031] Will adopt cupro ammonia viscose acetate jacquard fabric to dye blue flash gold in the present embodiment, its method is as follows:
[0032] 1. One-time washing: the fabric enters the jigger and washed 2 times. The washing temperature is 40°C, the washing time is 30min, and the water volume is 600L;
[0033] 2. The pretreatment solution configuration method is: sodium alkylbenzene sulfonate 10g / L, sodium dioctyl succinate sulfonate 3 g / L, pretreatment temperature 90°C, water volume 600L; 8 treatments;
[0034] 3. Secondary washing: hot water washing, temperature 95°C, 4 washings, 60 minutes of washing time, 2 cold water washings, 30 minutes of washing time, 600L of water;
[0035] 4. Acetic acid dyeing (fiber): Put the pretreated cupro ammonia viscose acetate jacquard fabric into the prepared disperse dyeing solution, and use the jigger method to dye the acetate fiber. The dyeing temperature is 70~98°C, and the dyeing time is For 90 minutes, the heating rate is 5°C per...
Embodiment 2
[0047] 1. One-time washing: the fabric enters the jigger and washed 2 times. The washing temperature is 40°C, the washing time is 30min, and the water volume is 600L;
[0048] 2. The pretreatment solution configuration method is: sodium alkylbenzene sulfonate 11g / L, sodium dioctyl succinate sulfonate 3.5 g / L, pretreatment temperature 88°C, water volume 600L; 8 treatments;
[0049] 3. Secondary washing: hot water washing, temperature 95°C, 4 washings, 60 minutes of washing time, 2 cold water washings, 30 minutes of washing time, 600L of water;
[0050] 4. Acetic acid dyeing (fiber): Put the pretreated cupro ammonia viscose acetate jacquard fabric into the prepared disperse dyeing solution, and use the jigger method to dye the acetate fiber. The dyeing temperature is 75~98°C, and the dyeing time is For 80min, the heating rate is 5°C per pass; until the end of the total dyeing time, the waste liquid is discharged; the disperse dye is prepared according to the following ratio, ac...
Embodiment 3
[0062] 1. One-time washing: the fabric enters the jigger and washed 2 times. The washing temperature is 42°C, the washing time is 30min, and the water volume is 600L;
[0063] 2. The pretreatment solution configuration method is: sodium alkylbenzene sulfonate 8g / L, sodium dioctyl succinate sulfonate 4g / L, pretreatment temperature 89°C, water volume 600L; 8 treatments;
[0064] 3. Secondary washing: hot water washing, temperature 95°C, 4 washings, 60 minutes of washing time, 2 cold water washings, 30 minutes of washing time, 600L of water;
[0065] 4. Acetic acid dyeing (fiber): Put the pretreated cupro ammonia viscose acetate jacquard fabric into the prepared disperse dyeing solution, and use the jigger method to dye the acetate fiber. The dyeing temperature is 80~98°C, and the dyeing time is For 60min, the heating rate is 5°C per pass; when the total dyeing time is over, the waste liquid is discharged; the disperse dye is prepared according to the following ratio, acetic aci...
PUM
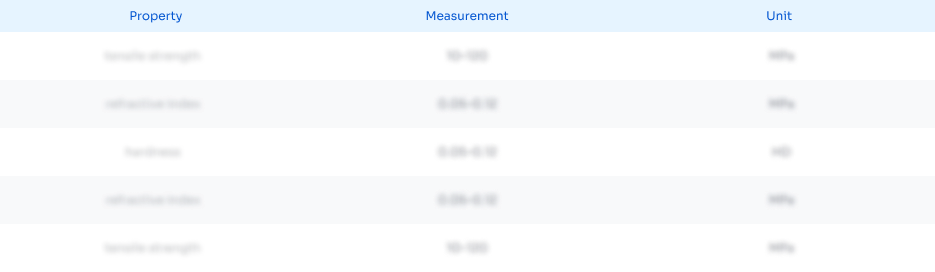
Abstract
Description
Claims
Application Information

- R&D Engineer
- R&D Manager
- IP Professional
- Industry Leading Data Capabilities
- Powerful AI technology
- Patent DNA Extraction
Browse by: Latest US Patents, China's latest patents, Technical Efficacy Thesaurus, Application Domain, Technology Topic, Popular Technical Reports.
© 2024 PatSnap. All rights reserved.Legal|Privacy policy|Modern Slavery Act Transparency Statement|Sitemap|About US| Contact US: help@patsnap.com