Novel permanent magnet alloy with composite low-price rare earth added and preparation method thereof
A permanent magnet alloy and rare earth permanent magnet technology, which is applied in the direction of magnetic materials, magnetic objects, and inorganic materials, can solve problems such as complex processes, and achieve simple preparation processes, easy implementation, and improved coercive force and temperature stability. Effect
- Summary
- Abstract
- Description
- Claims
- Application Information
AI Technical Summary
Problems solved by technology
Method used
Image
Examples
Embodiment 1
[0027] Step 1: By design composition (Gd 0.01 Ce 0.14 Nd 0.85 ) 30 Fe bal B 1.0 tm 1.1 (TM=Al, Co, Cu, Nb) (wt.%) Prepare raw materials, wherein the content of Gd accounts for 1% of the total amount of rare earths, and the content of Ce accounts for 14% of the total amount of rare earths.
[0028] Step 2: Melt the prepared raw materials to prepare quick-setting tape. First put the raw materials into the crucible of the quick-setting furnace, and conduct vacuum induction melting under the protection of argon. After the raw materials are fully melted to form an alloy, keep the temperature at 1300-1500 ° C, and pour the alloy liquid to a line speed of 1.0-2.0 m / s Prepare quick-setting sheets with an average thickness of 0.2-0.45mm on a water-cooled copper roller. The quick-setting tablet is made by Re 2 Fe 14 B columnar crystal main phase and flaky Nd-rich phase, the main phase columnar crystal is centered along the nucleation point of the roller surface, grows in a cone...
Embodiment 2
[0037] Step 1: By design composition (Gd 0.1 Ce 0.2 Nd 0.7 ) 31 Fe bal B 1.0 tm 1.1 (TM=Al, Co, Cu, Nb) (wt.%) Prepare raw materials, wherein the content of Gd accounts for 10% of the total amount of rare earths, and the content of Ce accounts for 20% of the total amount of rare earths.
[0038] Step 2: Melt the prepared raw materials to prepare quick-setting tape. First put the raw materials into the crucible of the quick-setting furnace, and carry out vacuum induction melting under the protection of argon. After the raw materials are fully melted to form an alloy, keep the temperature at 1300-1500 ° C, and pour the alloy liquid to a line speed of 1.0-3.0 m / s Prepare quick-setting sheets with an average thickness of 0.20-0.45mm on a water-cooled copper roller.
[0039] Step 3: crushing powder: (Gd obtained in the step 2 0.1 Ce 0.2 Nd 0.7 ) 31 Fe bal B 1.0 tm 1.1 (TM=Al, Co, Cu, Nb) (wt.%) The quick-setting sheet is put into the hydrogen breaking furnace, hydroge...
Embodiment 3
[0047] Step 1: By design composition (Gd 0.15 Ce 0.35 RE 0.5 ) 32 Fe bal B 1.01 tm 1.1 (RE=Pr, Nd; TM=Al, Cu, Zr) (wt.%) Prepare raw materials, wherein the content of Gd accounts for 15% of the total amount of rare earths, and the content of Ce accounts for 35% of the total amount of rare earths.
[0048] Step 2: Melt the prepared raw materials to prepare quick-setting tape. First put the raw materials into the crucible of the quick-setting furnace, and carry out vacuum induction melting under the protection of argon. After the raw materials are fully melted to form an alloy, keep the temperature at 1300-1500 ° C, and pour the alloy liquid to a line speed of 1.0-3.0 m / s Prepare quick-setting sheets with an average thickness of 0.20-0.45mm on a water-cooled copper roller.
[0049] Step 3: crushing powder: (Gd obtained in the step 2 0.15 Ce 0.35 RE 0.5 ) 32 Fe bal B 1.01 tm 1.1 (RE=Pr, Nd; TM=Al, Cu, Zr) (wt.%) The quick-setting sheet is put into the hydrogen break...
PUM
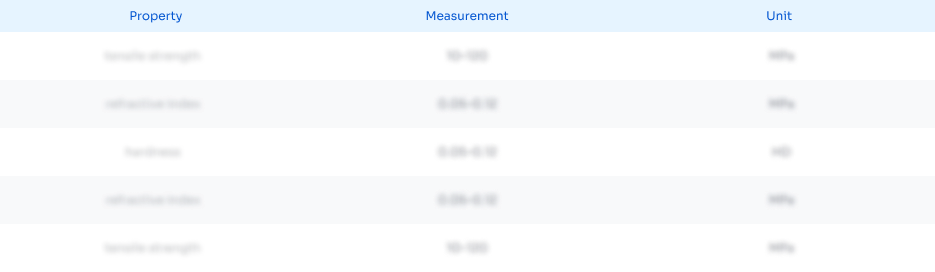
Abstract
Description
Claims
Application Information

- R&D
- Intellectual Property
- Life Sciences
- Materials
- Tech Scout
- Unparalleled Data Quality
- Higher Quality Content
- 60% Fewer Hallucinations
Browse by: Latest US Patents, China's latest patents, Technical Efficacy Thesaurus, Application Domain, Technology Topic, Popular Technical Reports.
© 2025 PatSnap. All rights reserved.Legal|Privacy policy|Modern Slavery Act Transparency Statement|Sitemap|About US| Contact US: help@patsnap.com