Composite filling material, preparing method thereof and application thereof
A technology of composite filling materials and flame retardants, which is applied in the field of composite filling materials and its preparation, can solve the problems of air permeability, weak anti-aging, anti-oxidation and impact resistance, affecting consumer perception, poor softness and comfort, etc. Achieve the effects of excellent processing performance and mechanical properties, excellent stability and wide application range
- Summary
- Abstract
- Description
- Claims
- Application Information
AI Technical Summary
Problems solved by technology
Method used
Image
Examples
Embodiment 1
[0032] The raw materials of the composite filling material are as follows:
[0033]
[0034] The preparation method of the composite filling material is as follows:
[0035] 1) Place polyethylene-octene copolymer, ethylene-vinyl acetate copolymer and azodicarbonamide in a container, mix and stir evenly, and then extrude through a single-screw extruder;
[0036] 2) During the extrusion process, add polyhydric reactive flame retardants, plasticizers, and antioxidants, extrude them into molds for vacuum setting, place them at room temperature to cool, and then cut and shape them according to requirements and directly fill them into mattresses use.
Embodiment 2
[0038] The raw materials of the composite filling material are as follows:
[0039]
[0040] The preparation method of the composite filling material is as follows:
[0041] 1) Put polyethylene-octene copolymer, ethylene-vinyl acetate copolymer, azodicarbonamide, and toluenesulfonyl hydrazide in a container, and mix and stir at a stirring rate of 300rad / min and a temperature of 30°C Extrude through a twin-screw extruder after uniformity for 20 minutes. The extrusion temperature is controlled at 150°C, the main engine frequency is 30Hz, and the screw diameter is controlled at 50mm;
[0042] 2) During the extrusion process, add dimethyl methyl phosphate, plasticizer, antioxidant, lubricant, and pH regulator and extrude into the mold for vacuum setting. At this time, the extrusion temperature of the twin-screw extruder is controlled at 140°C, main engine frequency 25Hz, screw diameter controlled at 55mm, then placed at room temperature and cooled to 25°C, cut and shaped accor...
Embodiment 3
[0044] The raw materials of the composite filling material are as follows:
[0045]
[0046] The preparation method of the composite filling material is as follows:
[0047] 1) Put polyethylene-octene copolymer, ethylene-vinyl acetate copolymer and toluenesulfonyl hydrazide in a container, mix and stir evenly for 30 minutes at a stirring rate of 200rad / min and a temperature of 45°C, and then pass through a twin-screw The extruder is used for extrusion, the extrusion temperature is controlled at 160°C, the main engine frequency is 20Hz, and the screw diameter is controlled at 60mm;
[0048] 2) During the extrusion process, add dimethyl methyl phosphate, halogen-free flame retardant, plasticizer, antioxidant, lubricant, 2-methyl-2-hydroxy-1-propanol and extrude into the mold Vacuum shaping. At this time, the extrusion temperature of the twin-screw extruder is controlled at 130°C, the frequency of the main engine is 28Hz, and the diameter of the screw is controlled at 60mm. T...
PUM
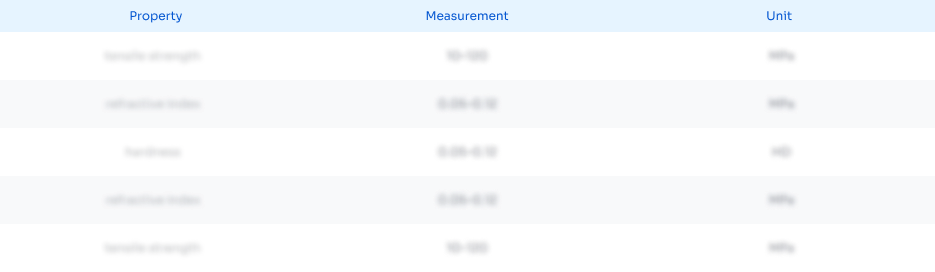
Abstract
Description
Claims
Application Information

- Generate Ideas
- Intellectual Property
- Life Sciences
- Materials
- Tech Scout
- Unparalleled Data Quality
- Higher Quality Content
- 60% Fewer Hallucinations
Browse by: Latest US Patents, China's latest patents, Technical Efficacy Thesaurus, Application Domain, Technology Topic, Popular Technical Reports.
© 2025 PatSnap. All rights reserved.Legal|Privacy policy|Modern Slavery Act Transparency Statement|Sitemap|About US| Contact US: help@patsnap.com