Silicate fireproof thermal insulation material and preparation method thereof
A fire-proof thermal insulation and silicate technology, applied in the field of fire-resistant materials, can solve the problems of poor thermal insulation effect, low compressive strength and high compressive strength, and achieve the effect of small bulk density, high compressive strength and improved compressive strength.
- Summary
- Abstract
- Description
- Claims
- Application Information
AI Technical Summary
Problems solved by technology
Method used
Image
Examples
Embodiment 1~3
[0032] According to the components and contents in Table 2, the following preparation methods were used to prepare the silicate fireproof and thermal insulation materials of the present examples 1-3:
[0033] (1) Sodium silicate and azodicarbonamide are mixed, fully stirred, sealed and stored, and placed at room temperature for 24 hours;
[0034] (2) Add hollow glass microspheres, colloidal silicon dioxide, sodium fluorosilicate, polyether glycol, and stir evenly;
[0035] (3) add diphenylmethane diisocyanate, stir;
[0036] (4) Pour the above-mentioned slurry into the mold, bake at a constant temperature of 150°C for 1.5h, then raise the temperature to 190°C, and bake at this temperature for 3h, then raise the temperature to 350°C, and bake at this temperature for 3h , After foaming and demoulding, the silicate fireproof and thermal insulation material can be obtained.
[0037] Table 2
[0038]
Embodiment 4~6
[0040] According to the components and contents in Table 3, the following preparation methods were used to prepare the silicate fireproof and thermal insulation materials of the present embodiment 4-6:
[0041] (1) Mix potassium silicate, azobisisobutyronitrile, and bis-azoaminobenzene, stir well, seal and store, and place at room temperature for 72 hours;
[0042] (2) Add hollow glass microspheres, colloidal silicon dioxide, sodium fluorosilicate, polyether glycol, and stir evenly;
[0043] (3) Add diphenylmethane diisocyanate, polyphenyl polymethylene polyisocyanate, stir;
[0044] (4) Pour the slurry obtained above into a mold, bake at a constant temperature of 160°C for 1 hour, then raise the temperature to 210°C, and bake at this temperature for 2 hours, then raise the temperature to 400°C, and bake at this temperature for 2 hours, After foam molding, the mold is demoulded, and the silicate fire-proof and heat-insulating material is obtained.
[0045] table 3
[0046] ...
PUM
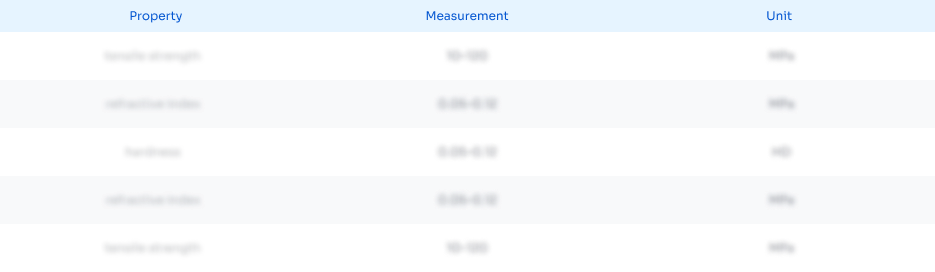
Abstract
Description
Claims
Application Information

- R&D Engineer
- R&D Manager
- IP Professional
- Industry Leading Data Capabilities
- Powerful AI technology
- Patent DNA Extraction
Browse by: Latest US Patents, China's latest patents, Technical Efficacy Thesaurus, Application Domain, Technology Topic, Popular Technical Reports.
© 2024 PatSnap. All rights reserved.Legal|Privacy policy|Modern Slavery Act Transparency Statement|Sitemap|About US| Contact US: help@patsnap.com